
一貫生産体制――「ねじ」1本にも本気で取り組むモノづくりへのこだわり
YKK APは素材や部品、生産設備から加工や組立に至るまでを自社で担う「一貫生産体制」を強みとしており、ねじまでも自社で生産しています。YKK APの「一貫生産体制」とはどのようなものか、またねじ1本にまでこだわり抜くYKK AP社員のモノづくりにかける想いについてお伝えします。
一貫生産体制 素材から部品、生産設備まで自社でつくる
YKK APの商品は、アルミや樹脂のフレーム、ガラス、網戸、機能部品など、さまざまなパーツからなりますが、それらのモノづくりのすべての工程を、自社の製造拠点で一貫して行っています。
主力商品である窓などに使われるガラスは素板の状態で仕入れ、自社でLow-Eガラスやトリプルガラスに加工。また、アルミ素材は地金の溶解から、樹脂素材は原材料の配合から、自社で行っています。商品の要ともいえる部品は、要素技術を含めた技術開発力をベースに、戸車、ねじ、網戸のネットなど、金属製・樹脂製の機能部品を生産。各種試験評価機能も有し、品質をより確かなものにしています。さらに、商品を生産する専用設備の開発・製造についても、工機技術部と呼ばれる自社の部門が担っており、工機技術部と開発・製造部門がシームレスかつ迅速に連携することで、技術競争力の一層の強化を図っています。
一貫生産にこだわるからこそ、スピーディな技術開発、サプライチェーン全体におけるコスト調整、確かな品質保証が可能になると考えています。

YKK APのモノづくりの根幹「一貫生産体制」
「木ねじ」の改良で施工時間短縮を実現
YKK APの「一貫生産体制」でのモノづくりへのこだわりは、ねじ1本にまで浸透しています。それを体現しているのが、2016年に行った木造住宅の躯体へ窓枠を取付ける際に使用する「木ねじ」の改良です。ねじ頭の十字穴の深さや、先端のねじ山形状を見直すことで、ドライバービットへの掛かりと木材への食い付き性を向上。ねじ留めの作業時間30%短縮(自社調べ)を可能にしました。
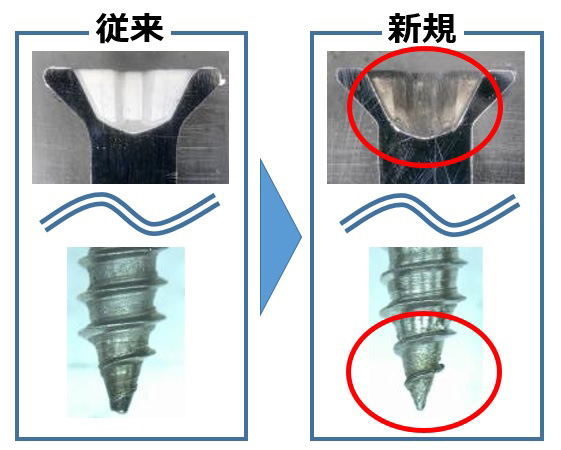
「木ねじ」の改良ポイント
・ねじ頭の十字穴の深さを見直し、ドライバービットとの掛かりを従来より深くすることで回転力が伝わり易くなりました。
・先端近くのねじ山の形状見直すことで、木材への食い付き性が向上しました。
自社でねじをつくる意味とは ねじ1本にかける社員の想い
ここからは、この「木ねじ」の改良に携わった、開発担当者の商品開発本部 PLM推進部長 須藤 良平さん(当時、窓商品の開発を担当)と、生産本部 黒部越湖製造所 金属部品製造課 ビスライン 総括ライン長 柴田 卓さん(当時、ねじの生産技術を担当)に、自社でねじをつくる意味や、ねじ1本にまでこだわり抜くモノづくりにかける想いについて聞きました。
一貫生産体制だからこそ導き出せる最適解
(須藤)この「木ねじ」の改良は、2017年4月に発売した基幹商品であるアルミ樹脂複合窓「エピソードNEO」の開発時に、商品の数あるセールスポイントの一つとしてねじにも優位性を持たせようと、既存のものよりも作業しやすい「木ねじ」へと改良しました。
そもそもねじはJIS規格で定められているため、それを満たしていれば一定の品質を担保することができます。しかし、本当にそれだけで良いのかを考えたときに、JIS規格内で満足するのではなく「より良いモノをつくりたい」という想いで、改良に着手しました。
まずは、ねじ山の形状や塗装の様子、先端の尖り具合などについて徹底的に調査。開発と製造が知識と技術を持ち寄り、改良を進めました。
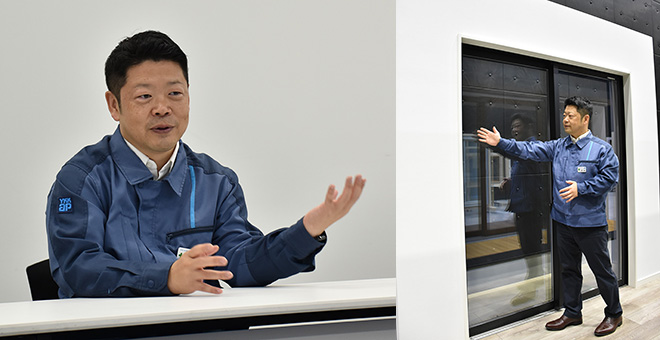
(左)須藤さん、(右)「木ねじ」を使用した窓商品
さらにYKK APには、商品開発や新たな商品価値の提供に不可欠な評価・検証を担う「価値検証センター」や、分析・解析に特化した部門など、社内にあらゆる専門部門があります。そういったところに協力を仰ぎながら、量産開始まで約3カ月という短い期間で形にすることができました。これだけスピード感を持って進行できたのは、開発、製造、品質、評価・検証、分析・解析などの社内の専門家が、近い距離感で密接に連携できる環境だったからこそだと考えています。外部業者を介していては、そうはいかなかったと思います。
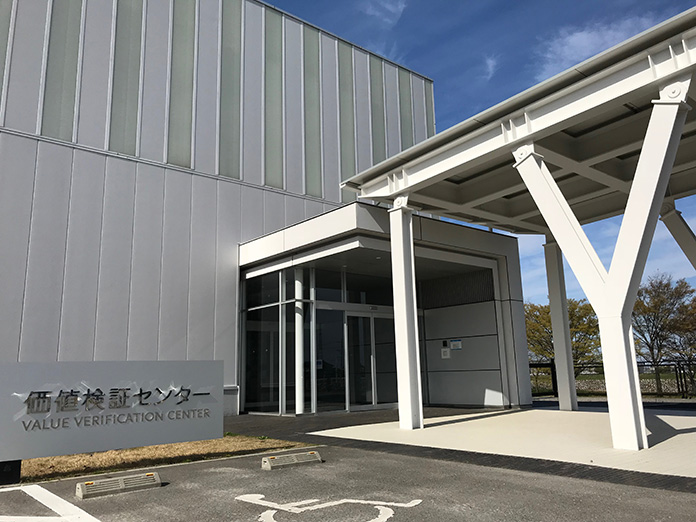
価値検証センター
さらに、品質やコストにおいても同様のことが言えます。いくら高品質で作業性の良いねじでも大きくコストがかかったり、製造工程上つくりにくい設計であってはいけません。また品質はお客様(「木ねじ」の場合は施工業者)が最終的に判断するものであり、他社比較や客観的な評価も含め社内のあらゆる専門部門を巻き込みながら設計段階からつくり込むことで、最適解を導き出すことができるのです。これは一貫生産体制だからこその強みであると考えています。
(柴田)生産技術担当者として「木ねじ」の改良に携わりました。当時を振り返ると、開発メンバーと一緒に自分たちで実際にねじを打ち、作業性の良し悪しを体感したり、商品への用途を理解したうえで「こういった特性が必要だから、こう改善しよう」「つくり方はこう変えてみよう」などと、密に会話したのを覚えています。
ねじは一般的に外部業者からでも調達することができます。でも、ほんとうに求めるねじを市場で見つけることができるかというと、そうはいきません。製造・開発がタッグを組み、商品の特性を十分に理解している私たちだからこそ、求める「木ねじ」を生み出すことができたのです。自社でねじをつくる意味はまさにこういうことなのだと、改めて実感しました。
全数検査でねじ1本の不良も見逃さない
(柴田)製造現場においても、徹底した品質への追求を行っています。YKK APのねじの製造を一手に担うビスラインでは、年間6億本ものねじを製造・出荷しています。これだけ膨大な数量のねじを製造する場合、抜き取り検査が一般的です。しかしYKK APでは、1本の不良も出さないという強い想いで、2017年から全数検査を導入しています。これは、高速カメラを使用したねじの画像検査と、袋詰めを自動で行うもの。不良を取り除くだけでなく、全数検査と袋詰めを連結して行うことにより、異品番のねじの混入を防ぐこともできるのです。
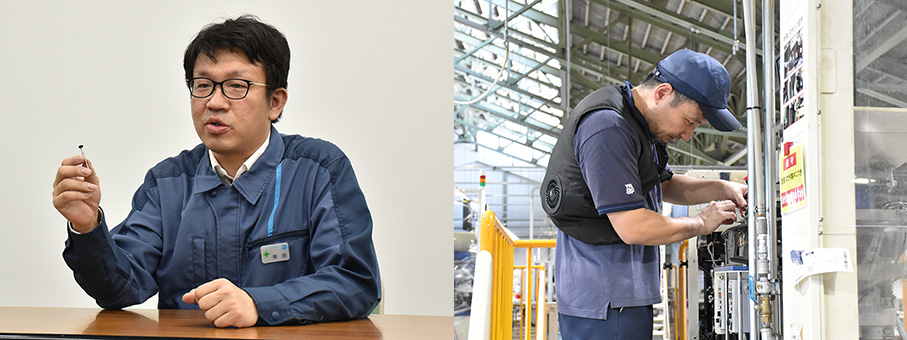
(左)柴田さん (右)全数検査装置の調整
設計段階で、たくさんの人が関わり技術が詰め込まれたねじ。「その技術を無駄にしないためにも、1本1本にこだわりたい」という社員の想いから、この全数検査装置の導入が実現しました。
そして、この装置によって不良としてはじかれたモノからデータを取るなど、不具合現象の確認から改善にもつなげています。
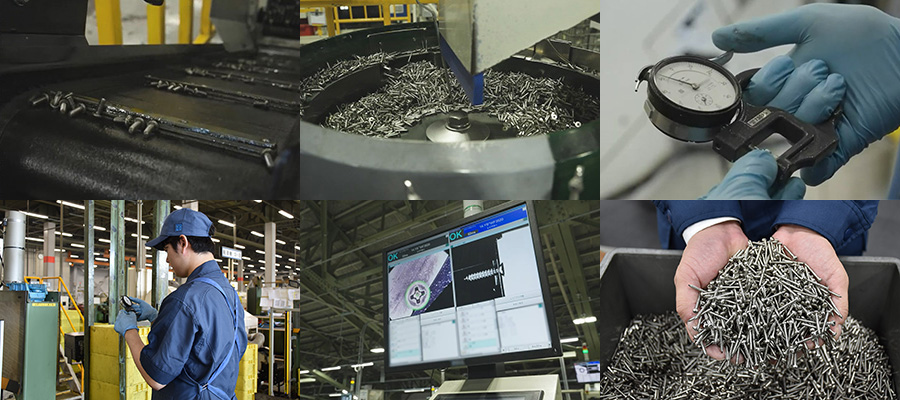
製造工程で1本1本に技術と想いが込められたねじ
「たかがねじ、されどねじ」ねじ1本にかけるYKK APの想いとは
(須藤)ねじは他の機能部品などと比べると地味な印象で、数ある部品の中でも小さく存在感は薄いかもしれません。しかし、「たかがねじ、されどねじ」。ねじ無くしては商品を組み立てることはできませんし、商品の性能を確保する上ではなくてはならない存在です。特に「木ねじ」は木造住宅に窓を取り付ける際に施工業者が使用するもので、その数は戸建住宅1棟あたり約700本※。この作業性が悪いと、商品やひいては会社の信頼を損なう恐れもあり、作業性改善は他社との差別化要素の一つとして、強く意識し取り組みました。商品で1番を追求するだけでなく、ねじでも1番を追求するのが、YKK APのモノづくりなのだと思います。
(柴田)つくり手の私たちからすると、年間製造本数6億本の中の1本かもしれませんが、そのねじを使用するお客様にとっては、大切な1本に違いありません。そのことを心に刻みながら、これからもモノづくりを追求していきます。
※戸建て住宅1棟あたり18窓取り付くモデルプランでの試算例。
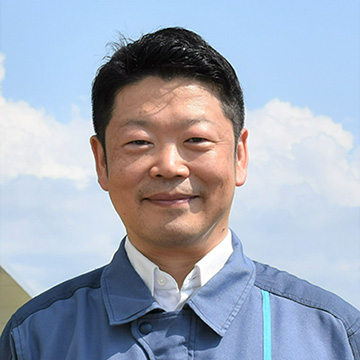
須藤 良平
1999年入社。商品開発を中心に担当。2017年度から業務本部にて新規開発プロセス(ECM)再構築を担当。2021年度から現職にて製品ライフサイクル管理基盤構築(PLM)を推進する。
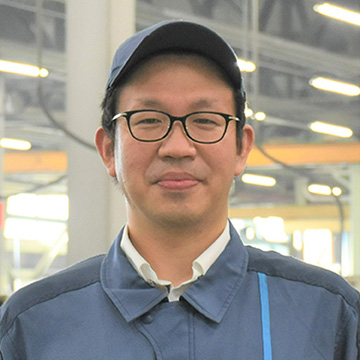
柴田 卓
2007年入社。ねじの生産技術を担当。2019年度から現職にて、ビスラインでねじの製造を統括・管理する。
この記事をシェアする
- SNSリンク X X シェアする
- SNSリンク Facebook Facebook シェアする
- SNSリンク LinkedIn LinkedIn シェアする
- SNSリンク LINE LINE シェアする
- コピーする リンクコピー リンクコピー リンクをコピーしました