
2050年までに環境負荷ゼロを目指すYKK APの“攻める環境管理”による資源循環のアクションとは
「Architectural Productsで社会を幸せにする会社。」をパーパスとして掲げるYKK AP。窓やドア、インテリア建材やエクステリア商品、カーテンウォールなどの商品の開発・製造・販売を通して幸せな社会をつくることを自らの存在意義として事業に取り組んでいます。今回は持続可能な社会の実現に向けた、環境との共生の取り組みについてお伝えします。
YKK APはビジョン「Evolution2030」の中で、「地球環境への貢献―脱炭素化・循環型社会実現に向けた仕組みづくり」を方針に掲げました。また、YKK APでは2050年の目指す姿として「事業活動におけるライフサイクル全体を通して“環境負荷ゼロ”を実現」を掲げており、2021年度~2024年度の中期環境政策では「気候変動」「資源循環」「水」「生物多様性」の4つの環境課題について目標を設定し、達成に向けて取り組んでいます。このうち「資源循環」では「樹脂窓(APW端材)社内リサイクル率100%(国内)」といった目標を定め、商品のライフサイクルを通じて廃棄物の発生を抑制するため、廃棄物発生要因を分析し、持続可能な資源の利用を進めています。
具体例として、以下のようなことに取り組んでいます。
- 発泡断熱材くずの体積を減容機の活用で7%にまで減少させてからリサイクル
- アクリル材くずを製造会社に返却して、再びYKK AP向けアクリル材の原材料の一部として使用
- 富山県内の4製造所合同で廃棄物を収集して固形燃料を191トン製造(2022年度)
そこで発泡断熱材、アクリル材の資源循環について富山県黒部市にある黒部荻生製造所で環境施設管理を担当する釣賀直哉さんに聞きました。
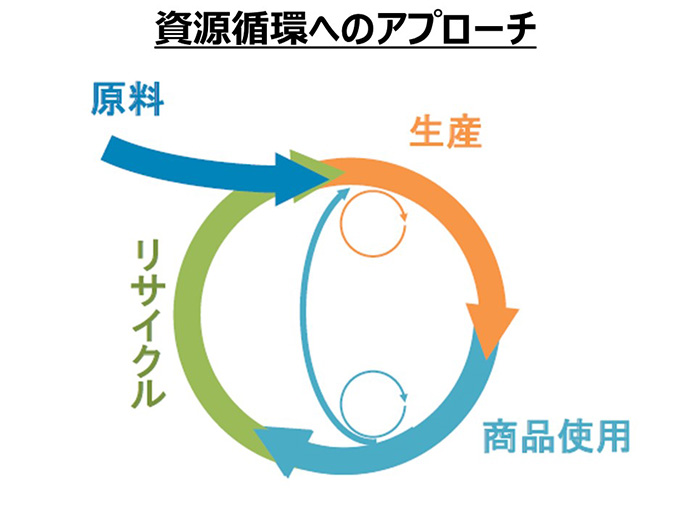
廃棄物を原料として再利用するマテリアルリサイクル
黒部荻生製造所では住宅用窓・窓用シャッターや、玄関ドア・引戸、インテリア建材などを製造しています。生産過程で主に廃プラスチックやガラスくず、木くず等の廃棄物が発生しますが、2022年度は2013年度比50.6%の排出量削減を達成しています。今後も継続して排出量を削減するために、黒部荻生製造所では廃棄物を原料として再利用する「マテリアルリサイクル」を推進しています。
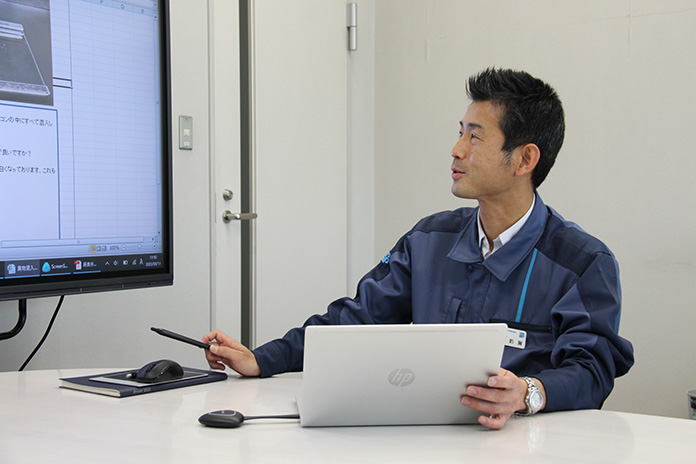
年間47トンの発泡断熱材をリサイクル
取り組みの1つが製品構成部材のマテリアルリサイクルです。YKK AP断熱玄関ドア「ヴェナート D30」では、合成樹脂の発泡断熱材を使用しています。発泡断熱材はドアのサイズやデザイン等の形状にあわせて加工され、毎月4トン、年間約47トンもの端材や加工くずが発生します。これらのくずは体積が大きくかさばるため、保管に大きなスペースが必要で、毎日大量に発生するため頻繁に回収しなければならず、運搬、回収に多額の費用がかかってしまいます。
発泡断熱材はリサイクル可能な材料ですが、処理にも課題があります。発泡断熱材は内部にたくさんの空気を含むため、そのままではプラスチック材料になりません。また軽いため、破砕したくずが飛び散ったり破砕機内に残り続ける等、処理にも手間がかかります。そのため他のプラスチックと比べて処理費用が高く、発泡断熱材をそのままの状態でマテリアルリサイクル、再資源化することは難しいと言われていました。
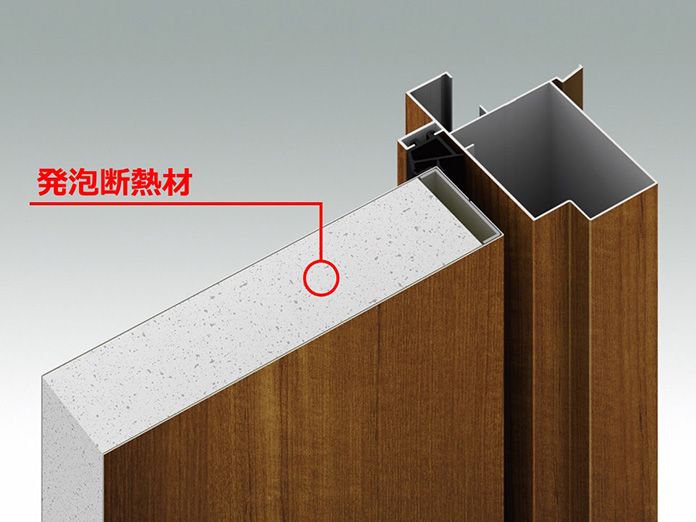
玄関ドア断面図(発泡断熱材を使用)
減容機で体積を10%以下に
そこで黒部荻生製造所では発泡断熱材のくずを「減容機」に入れて製造工程内で圧縮し、原料として回収、再利用しやすい形状に加工することでマテリアルリサイクルを実現しています。減容機は発泡断熱材を細かく砕いた後、温めることで空気が抜けて密度の高い塊(インゴット)になります。その結果、体積は減容前の7%にまで減少します(圧縮率93%)。またインゴットにすることで保管や運搬が容易になるだけでなく、材料の加工性も向上し、取り扱いがしやすくなります。インゴットは1週間で1立方メートルの袋に4袋程の量になり、食品トレーなどプラスチック材料を扱う会社に有価物として売却しています。
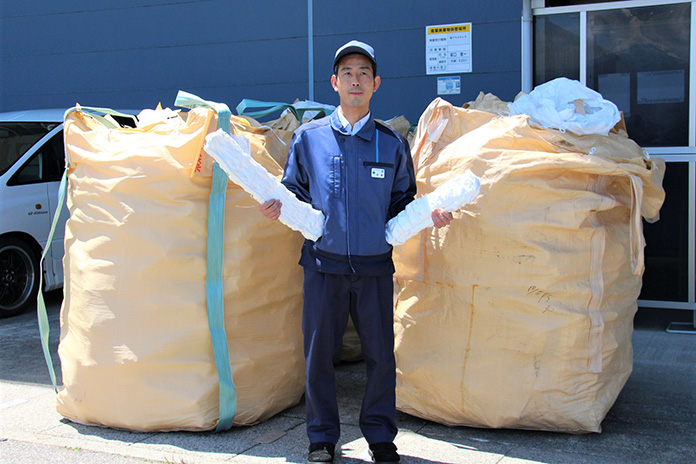
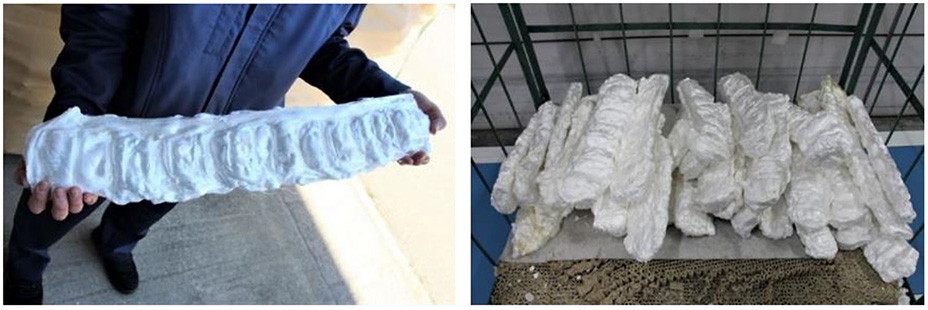
減容後の発泡断熱材くず
圧縮されて固くなり、省スペースのため管理も容易に
廃棄物を再び製品へ
もう1つの取り組みが廃棄物の循環利用で、製造時に出たアクリル材のくずを再びアクリル材にして、利用しています。インテリア建材の一つで、室内空間を仕切る「スクリーンパーティション」ではアクリル材を使用しており、製造工程で発生する端材は全て回収し、マテリアルリサイクルをしています。その中でも、指定品番のアクリル端材は製造会社に返却し、YKK AP向けアクリル材の原材料の一部として使用しています。製造元に返却するアクリル材は年間約26トンにもなり、資源の循環、有効活用につながっています。アクリル材の循環利用を実現するためには、返却するアクリル材の品質管理に苦労しました。当然ですがリターン材(返却端材)に不純物が混ざっていると回収ができないからです。製造元と協議した際にも「ホコリや変色があるリターン材は使い物にならないため取り扱いを見直してください」と指摘いただき、分別基準を見直した上で計画通りの回収ができるように体制を整備しました。ホコリよけ用の保護フィルムがはがれないよう慎重に扱い、回収品の見回り・点検も工程に組み込み、作業や表示の現場担当者の方への周知を徹底しました。
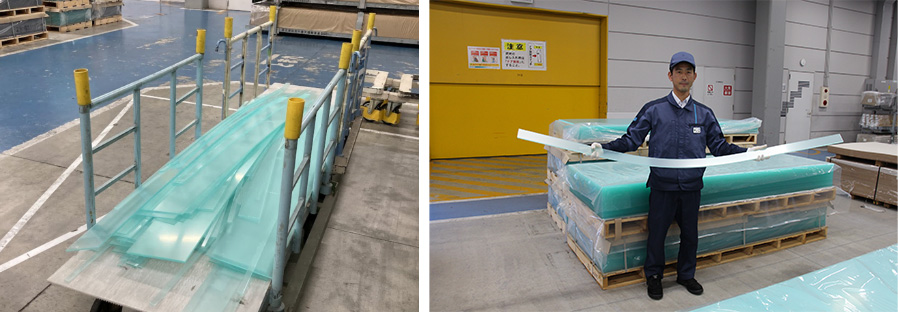
廃棄物に付加価値をつける
現在、発泡断熱材、アクリル材については黒部荻生製造所でのリサイクル率100%を達成していますが、資源循環については課題もあります。複合素材や新たな開発材料が登場し、廃棄物はますます多様化するとともに処理が難しくなっています。そのままではリサイクルができない物も減容化や、利用可能な材料の選別をするなど付加価値をつけることで再資源化できる可能性があります。廃棄物や有価物の処理を委託業者任せにはせず、自社で前処理や加工を施す取り組みが今後は重要になると思います。
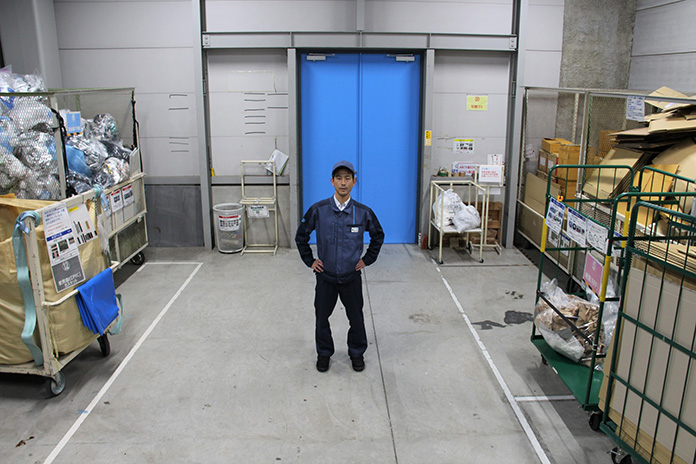
廃棄物が固形燃料に生まれ変わる
廃プラスチックの「マテリアルリサイクル」を推進する一方、黒部越湖製造所では廃プラスチックを「有価物化」により、廃棄物の削減を進めています。この取り組みについて黒部越湖製造所における環境管理施設の責任者である荒木修さんに話を聞きました。
部品生産の主要拠点として、ねじやハンドル、網戸のネットまで多種多様な部品を生産している黒部越湖製造所。生産過程で黒部荻生製造所と同様に廃プラスチックやガラスくず等の廃棄物が多く出ますが、廃棄物分別の徹底などの継続により2022年度は2013年度比57%の削減を達成しました。今後も削減を進めるため目を付けたのが、廃棄物を固形燃料にするRPFの製造です。
RPFはRefuse derived paper and plastics densified Fuelの略称で、「廃プラスチック、古紙を原材料とした固形燃料」です。RPFの製造により廃棄物を有価物にして売却できるほか、化石燃料の削減によるカーボンニュートラルにも貢献できます。黒部越湖製造所では主にガスケット(窓ガラスをサッシに止め付けるゴム)屑が原材料になります。原材料を破砕し、選別機が異物を除去した後、材料に熱を加えて、成形機で圧縮するとRPFが完成します。投入した廃棄物量に対してほぼ100%のリサイクルが可能です。
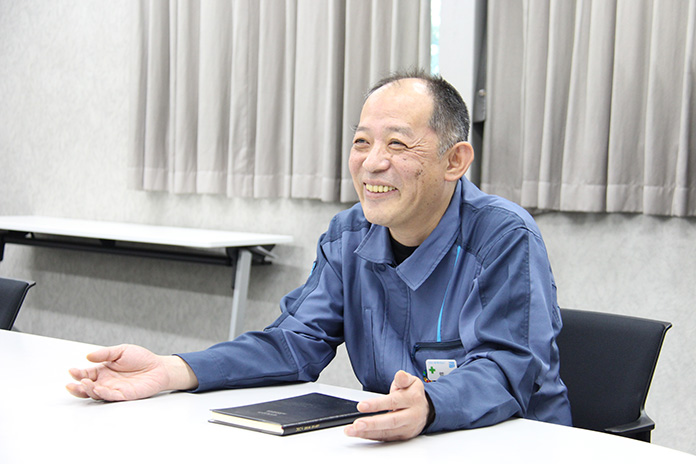
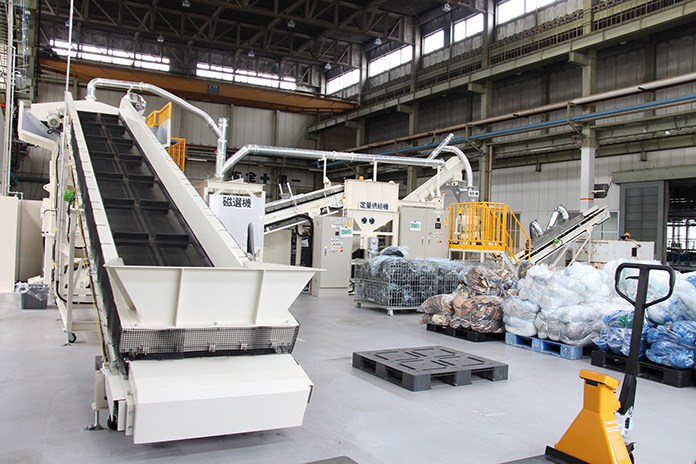
RPF製造設備
一製造所だけでは設備が導入できない
ただ、RPF製造設備を導入するにあたり、黒部越湖製造所の廃棄物の量だけではRPFの生産能力を十分に発揮することが難しい状況でした。そのため自製造所だけではなく、同じ富山県にある黒部製造所、黒部荻生製造所、滑川製造所と合同で廃棄物を収集して、RPF製造を行う計画を立てました。当初は導入を不安視する声もあり、私自身が各製造所に行き、実際に廃棄物を見てRPFの原材料にできるのかサンプルを集めて検討しました。行動することで「皆で決めた事は皆でやる」という意思を示して、各製造所を巻き込んでいきました。
燃料の燃え方を左右する「レシピ」づくりに苦心
苦労したのはRPFの購入先が希望するRPFの「レシピ」作成です。RPFは投入する材料とその割合によって燃え方が異なります。材料に紙が多いと燃えすぎて取引先の設備では使いにくくなり、ガスケット屑を多くすると大気汚染の原因になるSOx(硫黄酸化物)等の排出につながります。
またRPFに含める廃棄物の種類が多くなればその分レシピも複雑になります。このため、各製造所からの廃棄物を組み合わせたRPFの製造には試作品をつくり、希望通りに燃焼するかの分析が欠かせませんでした。希望の燃え方に合う試作・分析を何度も繰り返した結果、軟質廃プラスチック30%、硬質廃プラスチック30%、紙類40%の割合で作成するレシピが完成。原材料となる廃棄物は黒部製造所40%、黒部越湖製造所30%、黒部荻生製造所25%、滑川製造所5%の割合で収集する体制を構築しました。
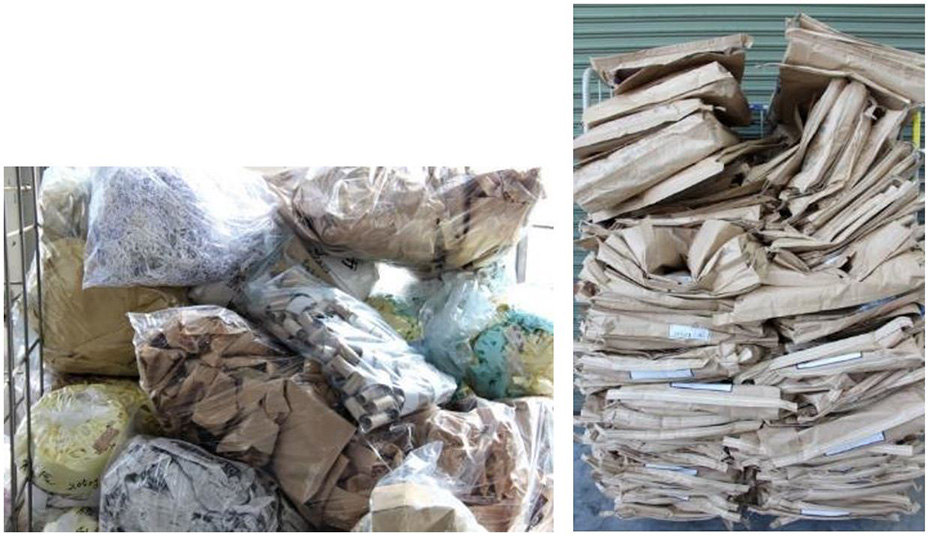
周辺エリアにある製造所からも廃棄物を収集
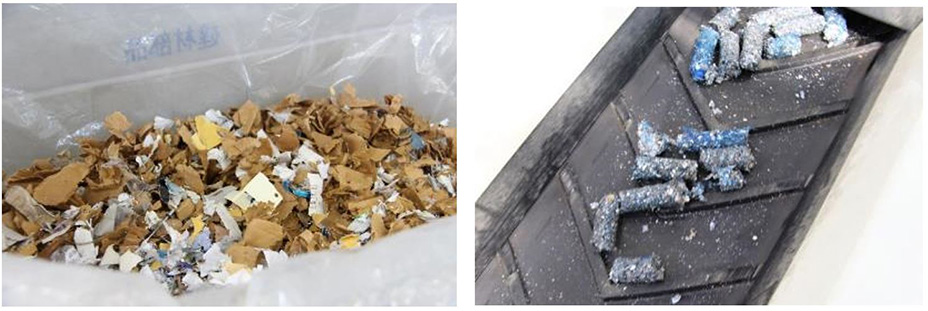
作成したレシピの割合で廃棄物を破砕、圧縮
想定を上回るRPF生産量に
廃棄物の収集体制の整備、製造レシピの完成によりRPF製造機(生産能力150kg/h)を2022年2月に導入できました。導入後、廃棄物の削減効果が実感できると4製造所の一体的な取り組みとして活動も定着し、2022年度は155トンのRPF生産計画に対し、191トンを製造し、売却しました。2023年度は203トンの生産計画ですが、現在廃棄物の収集体制を全国の製造拠点に広げて、最終的に300トンの生産ができないか検討を重ねています。実現には廃棄物運搬の許認可や、運送コストとの兼ね合いなど課題はありますが、地域の枠を超えて製造部門全体で価値創出をしたいと思います。また将来は生産したRPFを製造所内のボイラー燃料にするなど自家消費型の利用を検討しています。
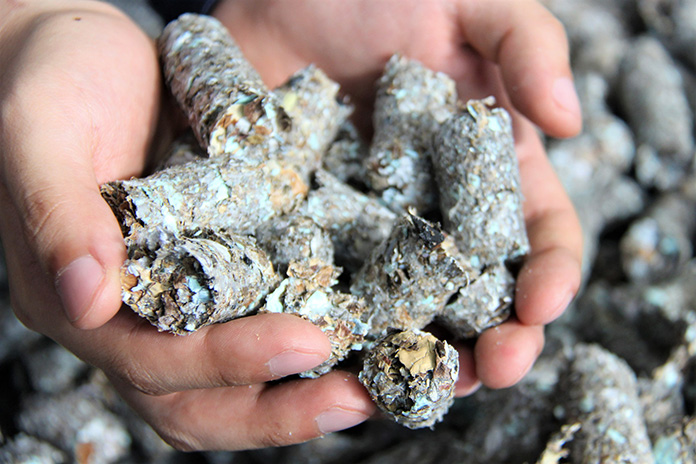
完成したRPF
攻めの環境価値創出
一製造所の環境管理者としてここまで踏み込んだ設備投資ができるのは、資源循環に対する会社の明確な環境方針があるからです。安全環境管理はリスクに対する法令遵守や社会に向けた対応で絶対に守るべき基準があります。そのために守りを固めるのは当然ですが、そこに留まらず、さらに踏み込み、“攻める”環境管理をしていきます。攻めの姿勢を示さないと2030年、2050年の高い環境目標を超えることは難しいです。手を挙げられる拠点がリーダーシップを取って他の拠点を巻き込み、環境課題の達成に貢献していきます。
YKK APは2050年に目指す姿の達成に向け、ライフサイクルの全ての段階で環境価値を創出できるよう、環境負荷低減活動を実践しています。こうした取り組みを「エコ・ファーストの約束」として宣言し、2023 年4 月には環境省が環境分野において「先進的、独自的でかつ業界をリードする事業活動」を行っている企業であることを認定する「エコ・ファースト企業制度」において「エコ・ファースト企業」に認定されました。YKK APでは今後も、次世代に対してより良い社会・環境をつくるために、技術革新による新しい価値の創造に挑戦しています。
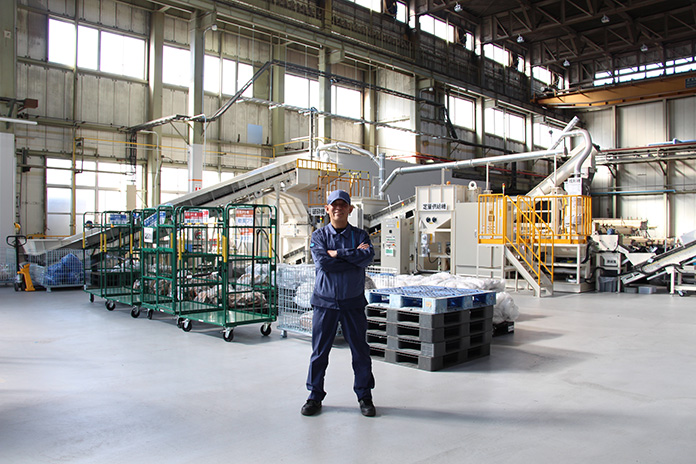
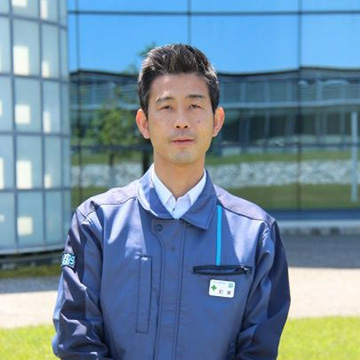
釣賀 直哉
2004年入社。黒部荻生工場 エントランス製造部 生産技術室でラインや生産性改善業務に従事。
2007年環境施設管理室に異動。黒部荻生製造所の主担当者として省エネルギー推進や廃棄物の管理、環境法規制対応等に取り組み現在に至る。廃棄物の管理では埋め立て廃棄物のゼロ化、製造工程の廃棄物削減、リサイクルの推進を担当している。
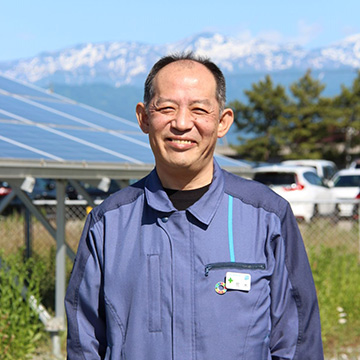
荒木 修
1985年入社。黒部越湖工場にて部品製造・生産技術・ライン管理・生産管理に従事。
2018年度から現在の役職にて越湖製造所の安全衛生・環境・施設の管理を担当している。
この記事をシェアする
- SNSリンク X X シェアする
- SNSリンク Facebook Facebook シェアする
- SNSリンク LinkedIn LinkedIn シェアする
- SNSリンク LINE LINE シェアする
- コピーする リンクコピー リンクコピー リンクをコピーしました