
Recreating heavy rain, storms, and other harsh natural environments for verification. “Field verification” initiatives to provide product value through reliable quality and performance evaluation.
YKK AP’s Purpose is "We Build a Better Society Through Architectural Products;" building a better society through developing, manufacturing, and selling products such as windows, doors, interior architectural products, exterior products, and curtain walls is the meaning and purpose of our business. In this article, we will talk about our "field verification" initiatives. These take place in our technical facilities, where we evaluate and verify our products, through the recreation of real-life environments.
YKK AP’s 6th Mid-term Business Policy (FY2021 to FY2024) includes "Providing Social Value through Products and Realizing Manufacturing Reform." To provide products that meet the demands of society, including safety, health, disaster prevention, energy conservation, and others, and to contribute to the sustainable development of society, the creation of technology that supports monozukuri (manufacturing) is vital. At the Value Verification Center, a technical facility where we carry out one of the processes involved in creating technology—the evaluation and verification of products—we recreate a variety of real-life environments to verify our products, obtaining a wide range of knowledge and data and acting to make use of this in our products. We asked Head of the Real-life Environmental Quality Promotion Office Yutaka Ihara and Takahiro Nishitani, who are responsible for real-life environmental verification at the Value Verification Center, about some specific initiatives.
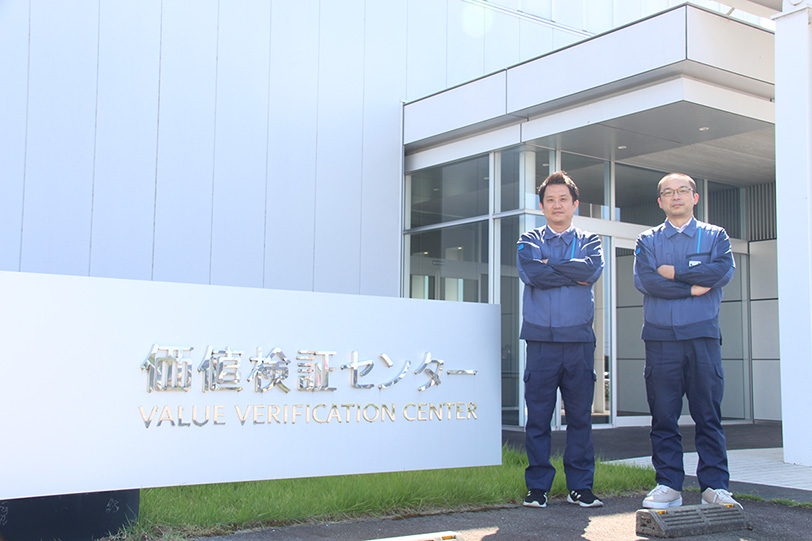
(Left) Mr. Ihara (Right) Mr. Nishitani
Confirming reliable quality and performance in real-life environments
The Value Verification Center (VVC) was established in 2007 as a facility for the evaluation and verification of the value of products from the perspective of the people who will actually use those products. It finds hidden issues and problems with usability through "field verification," which recreates harsh natural environments, and "user verification," carried out by consumer monitors, which recreates environments from day-to-day life, confirming product performance from the design stage to product receipt and long-term safe use by customers. Of these, the field verifications for which we are responsible include evaluation and verification through the use of equipment within the facility to determine whether a product satisfies the performance standards we require.
There are a variety of public standards in society, including the Japanese Industrial Standards (JIS), but we have established in-house standards that ensure basic performance while being stricter than these public standards according to necessity; moreover, in cases where we judge quality inspection to be required but there are no standards, we establish new in-house standards and carry out evaluations and verification. Our role includes the creation of standards and methods for evaluation and verification in such cases.
We share knowledge with developers and engineers to verify the environmental conditions in which products are used and their possibilities until we are satisfied, so as to provide product value that exceeds expectations.
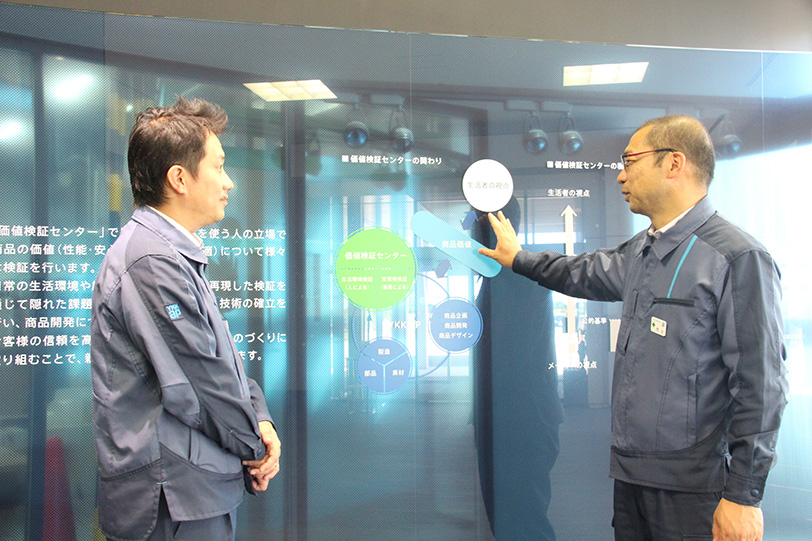
Recreating various environments, including heavy rain and storms
More specifically, in the case of windows, we will use testing equipment to evaluate and verify their basic performance, including watertight performance, airtight performance, and sound insulation. When verifying watertight performance, which demonstrates to what extent a window prevents rainwater from entering a room, we spray four liters of water per square meter to confirm that water will not enter a room even during heavy rain. For example, we have verified that our vinyl window "APW 330," which has a JIS watertight performance grade W-4, does not let in rainwater even with wind pressure equivalent to windspeeds of 16–29 m/s.
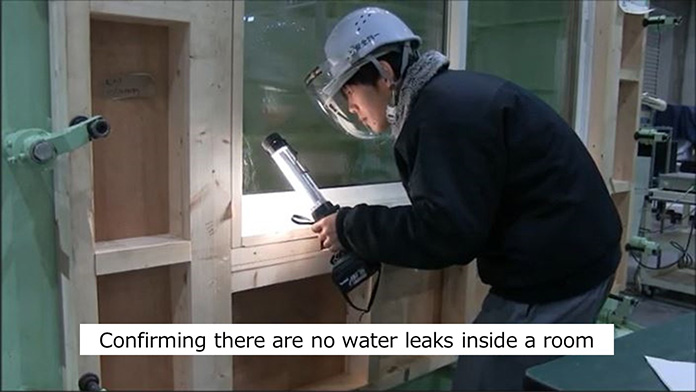
Verifying the watertight performance of a window
In addition, when it comes to verifying watertight performance and airtight performance, we have set up an enormous wind-tunnel device that is capable of generating strong wind and rain. We use this device to plan for residential environments in which people actually live and verify that nothing will enter a room from the window during a storm or dust cloud.
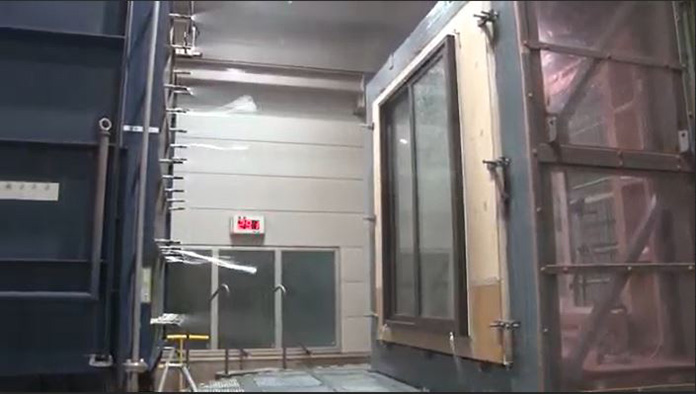
Verifying watertight performance by recreating a storm
On top of this, we are also able to use this wind-tunnel equipment for other verification, including strength when an entrance door or a window is blown by wind, and whether there is a wind noise from the door or window. JIS does not specify testing with actual wind, but here we can recreate real-life environments during strong winds and verify the components and closers that restrict opening when an entrance door or window is wind-blown.
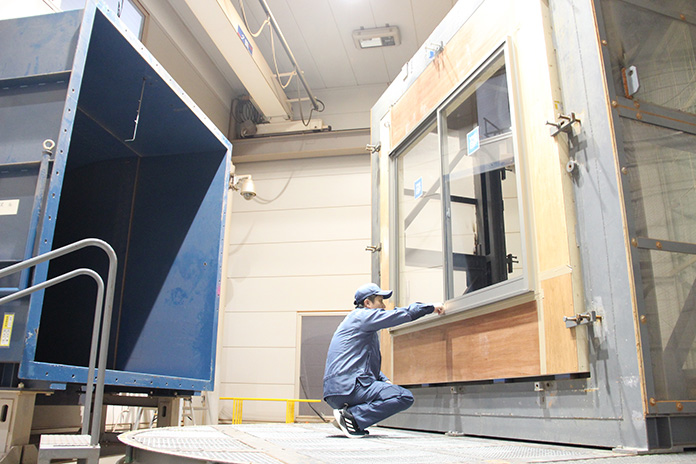
Our role also includes verifying increased reproducibility in accordance with the current environment, leading to the discovery of new issues and the establishment of new technology. Over several years, we have carried out evaluations and verification in response to increasingly severe natural disasters, such as large typhoons and torrential rainfall; there were some initiatives among these that left an impression.
Window shutters that had no impact resistance standards against flying debris
In 2018, a number of large typhoons hit the Kansai region in particular; Typhoon No. 21 reached a maximum windspeed of 58.1 m/s at Kansai International Airport, the highest figure in history. These strong winds caused severe building damage, and there were scattered cases of damage to window glass from flying debris such as broken signboards and exterior materials from buildings.
During these events, windows with shutters received little damage, enabling us to confirm that shutters play an important role in protecting windows. However, at the time there were no clear standards in the company or the industry to demonstrate how strong shutters need to be against flying debris. Thus, we had to establish new standards for evaluation and verification, as well as techniques to accomplish this.
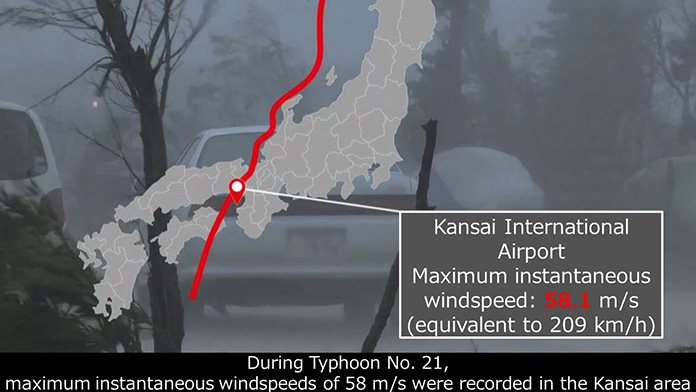
Establishing evaluation standards in cooperation with an external expert
When we were determining the standards and techniques for evaluation and verification, we hoped to refer to the knowledge of an external expert as well as our in-house knowledge, so we contacted Professor Takashi Maruyama of the Disaster Prevention Research Institute, Kyoto University, who is engaged in research on the theme of wind-resistant construction. As we received his advice and worked together to establish standards to verify the impact resistance of shutters against flying debris, the tiles on the roofs of residences and other buildings left an impression. These tiles are heavy and hard, and in areas with strong winds from typhoons, instantaneous windspeeds of more than 30 m/s mean they can come off roofs, so we were told we must verify these as flying debris. And so, we decided to use experimental methods in accordance with the "test methods for flying debris impacts during storms for glass for buildings" established as JIS in 2018 and the values of the international ASTM Standards as a base to verify the impact resistance of shutters, with the addition of tiles. As a result, we were able to confirm that when the shutter was closed, our window glass did not break even when it was hit with a 2.05 kg wooden material traveling at 12.2 m/s (44 km/h), representing flying debris equivalent to a fragmented roof tile.
Verifying a shutter hit by a tile

Verifying a shutter hit by a wooden material

The outcomes of this verification enabled us to once again recognize the performance of shutters in protecting window glass from flying debris during strong winds and storms. Based on the verification results, in 2020 we launched "GR wind-resistant shutters," which have wind resistance performance two ranks higher than standard shutters (1,200 Pa), and significant strength against impacts from flying debris.
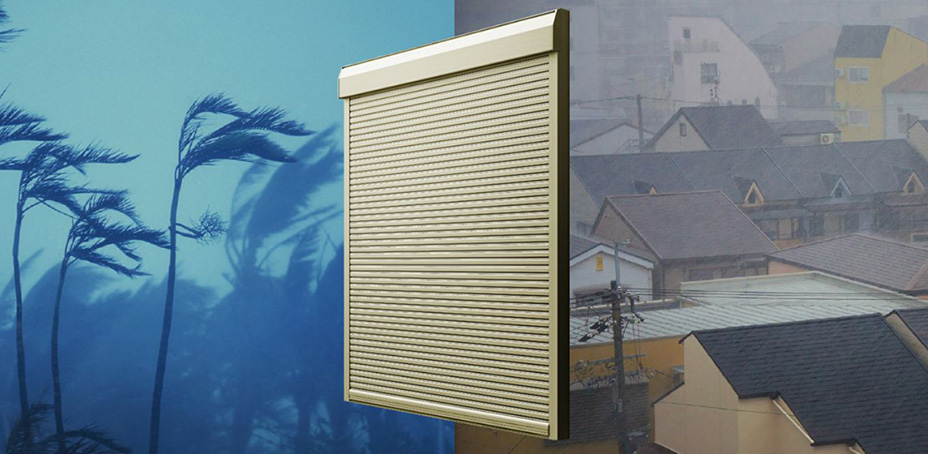
GR wind-resistant shutters
When there are no standards representing product performance, we will need to establish new standards and ways of verifying these in the future, similar to the performance evaluations of the shutters against flying debris. The advantage of setting standards and carrying out evaluations and verification is that we can clearly demonstrate performance and value that is difficult to see and comprehend. In the future, the Value Verification Center will not only engage in verifying the value of products, but also share information so people can understand that verified value.
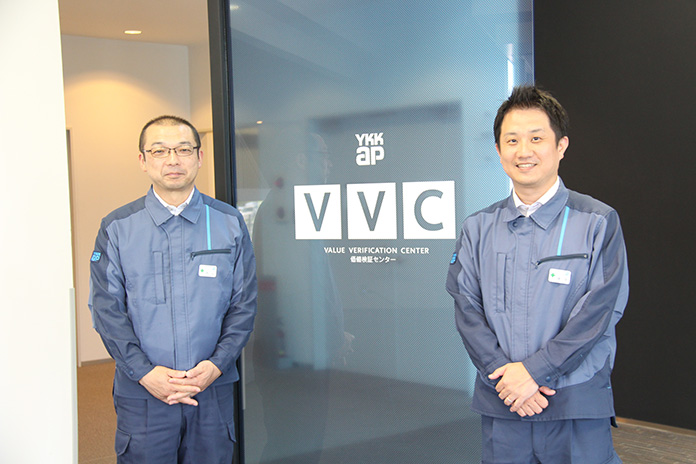
At the Value Verification Center, YKK AP engages in initiatives for verification and standard creation through "field verification," in preparation for natural disasters, as well as "user verification," which emphasizes day-to-day living environments; these have been appraised, and in 2017 we won a third "Product Safety Award" in the Manufacturer and importer division, major companies from the Ministry of Economy, Trade and Industry for excellent initiatives for product safety. We were certified as a "gold product safety company," and this certification continues in 2023. We will continue being thorough in our product evaluations and verification when it comes to various risks that could occur during the commercialization process and during use, working to realize a high level of safety, and strive to provide products that people can use with peace of mind.
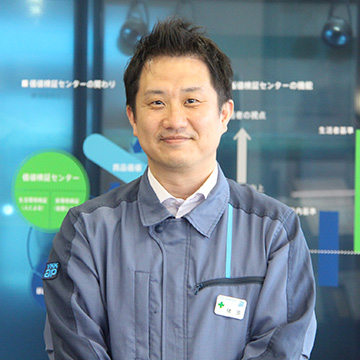
Yutaka Ihara
He joined the company in 2020, and since then has worked to evaluate the installation of new products at the Value Verification Center. From 2023, he has been responsible for promoting real-life environmental quality in his current role.
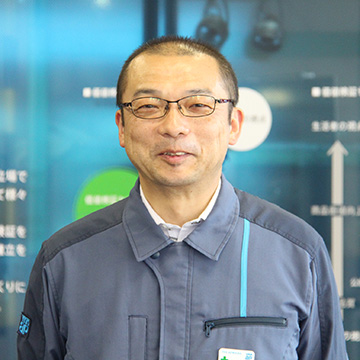
Takahiro Nishitani
He joined the company in 1998. After developing window products for residential use, in 2009 he moved to the Real-life Environmental Quality Promotion Office in the Value Verification Center. Through performance evaluations, he has striven to carry out verification that will lead to product predominance, the visualization of outcomes, product development, and product proposals.
Share this article
- SNS Link X X Share
- SNS Link Facebook Facebook Share
- SNS Link LinkedIn LinkedIn Share
- SNS Link LINE LINE Share
- Copy Link Copy Link Copy Link Copied Link
Related stories
-
The Evolution of the Aluminum Profile Department into the Automotive Industry’s Manufacturer of Choice
- Aluminum Profile
- Technology
- Sustainability
- Solving Social Issues
-
Toward Achieving Carbon Neutrality: Taking on the Challenge of 100% Aluminum Recycling by a Window Manufacturer
- Technology
- Manufacturing
- Environment
- Sustainability
-
Stop the Landfill Disposal of Used Vinyl Windows! Disseminating Vision for Vinyl Window Recycling Through Industry-Government-Academia Collaboration, and Taking on the Challenge of "Window-to-Window" Recycling
- Technology
- Manufacturing
- Environment
- Solving Social Issues