
The Evolution of the Aluminum Profile Department into the Automotive Industry’s Manufacturer of Choice
In addition to products for residential and commercial buildings such as windows and doors, YKK AP is also engaged in the business of selling aluminum profiles as components / member for customers to make their own brand products, taking advantage of the technical expertise it has cultivated as an aluminum manufacturer. This article gives an overview of the challenges that the Aluminum Profile Department, which handles this Aluminum Profile Business, and its efforts to achieve carbon neutrality in auto parts.
Business Activities of the Aluminum Profile Department
Origins of the Aluminum Profile Business
The Aluminum Profile Business was launched in 1999, and began selling aluminum profiles for non-YKK products in order to utilize excess production capacity in manufacturing equipment for the company’s mainstay aluminum products such as fasteners, windows, and doors. Since YKK AP is also a manufacturer of architectural products, production first began in the construction field, such as roof coping.
What is the Aluminum Profile Business?
The Aluminum Profile Business provides aluminum as bar profiles for customers’ applications. In the casting process for bar profiles, a certain amount of metals such as magnesium and silicon are mixed in with aluminum ingots, which serve as raw materials, and are melted in a melting furnace to cast "billets," which are cylindrical ingots. Next, in the extrusion process, the billets are cut to a certain length, heated at high temperature, and loaded into the extruder. YKK AP mainly sells aluminum bar profiles, which is extruded successively under high pressure, heat treated for strength, and colored in the surface treatment process. The aluminum bar profiles is then cut and processed at the customer’s end, but if the customer is unable to do this, we can also cut and process it in-house before sale.
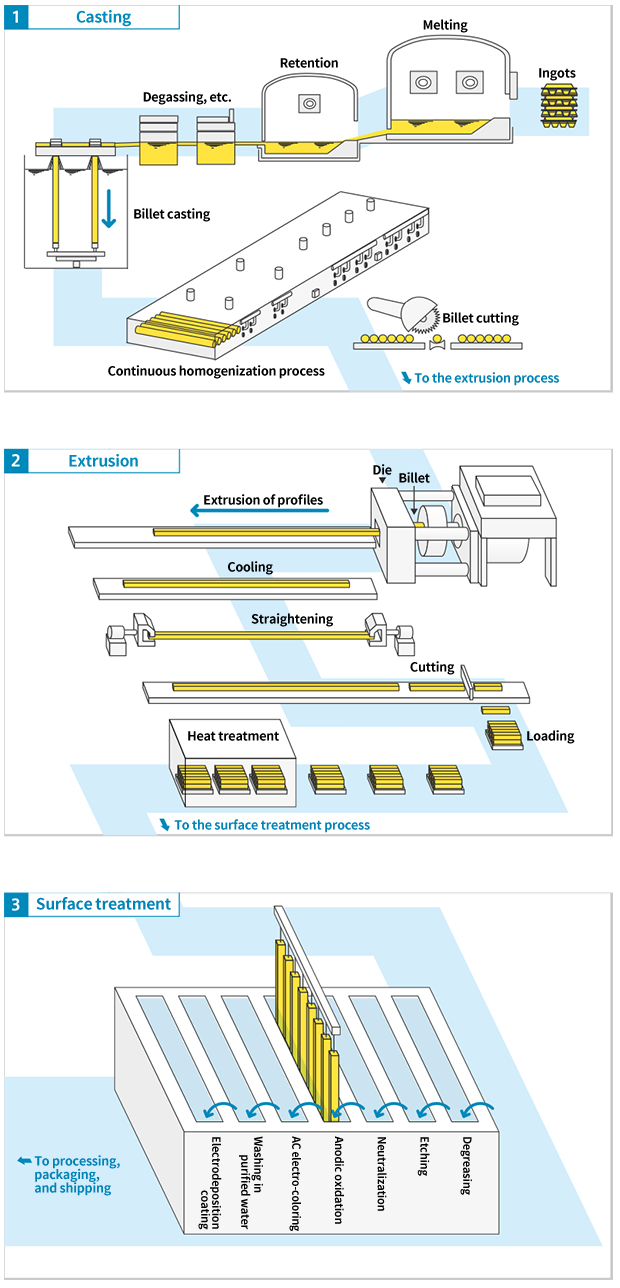
Aluminum profile (aluminum bar profiles) manufacturing process
Currently, more than 60% of our main business partners are companies in the construction field, such as those dealing with exteriors and interior / exterior materials. The remaining 40% or so come from a wide variety of industries and companies, including the transportation sector for passenger cars and trucks, the electrical and machinery sector for motor frames and machine frames, and the metal products sector for system kitchens, ladders and stepladders. Our goal is to increase the proportion accounted for by fields other than architectural products, including transportation, electrical machinery and machinery, to just under 50% by around 2030.
New Challenges for Realizing a Sustainable Society
The aluminum profile industry has been undergoing change in recent years. In the domestic market, demand in the construction sector has been shrinking year by year, due in part to the declining population. On the other hand, the transportation sector, including the automotive field, is growing, and there is an increasing demand for more versatile and sophisticated end products made of aluminum. For example, by modifying the cross-sectional shape of a member, it can function to absorb impact in the event of a collision, rather than simply serving as a structural element. In addition, cost competition is becoming increasingly intense due to the rise of overseas manufacturers. The Aluminum Profile Department, while focusing on the construction sector, which has always been its core area, has also made aggressive inroads into fields other than architectural products, such as transportation, electrical machinery, and machinery. We asked Takeshi Teraki, Vice President and Head of the Aluminum Profile Department, about the company’s initiatives in Auto parts, which have been a major focus in recent years.
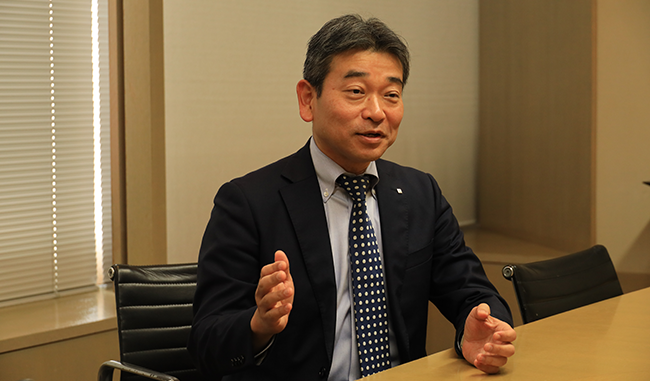
Reasons for Entering the Automotive Industry
It all started when a purchasing manager at an automotive manufacturer and a YKK AP (then YKK) sales representative lived near each other, and through their friendship, the former became aware that YKK AP also handled aluminum products. Generally, improving the fuel efficiency of vehicles often requires reducing the weight of the body, which requires lighter aluminum. However, after subsequent meetings were held and more dialogue took place, it became clear that rather than simply supplying materials, we needed to accommodate the client’s various requests. For example, they required not only processing technologies such as bending, which YKK AP already possessed and used in the manufacture of its own products, but also aluminum welding technology. Accordingly, we purchased an aluminum welding machine, and through repeated trial and error in the technology divisions, made efforts to improve our aluminum welding technology. Thanks in part to this, the decision was made to use aluminum profiles for part of the frame of a hybrid vehicle, which required technical expertise, even though gasoline-powered vehicles were still dominant at the time. This deal led to more opportunities to talk directly with designers from various automobile manufacturers, and because of our advantages over other companies in terms of molding technology for 6000 series alloy (*1) extrusions, CAE analysis (*2) of components, and cost, our business with the automobile industry has increased since then, leading to what it is today.
Initiatives to Solve Current Issues in the Automotive Industry
The Japanese government has declared its commitment to achieving carbon neutrality by 2050. As part of this initiative, comprehensive measures will be taken to increase the percentage of new passenger car sales accounted for by electrically-powered vehicles (*3) to 100% by 2035.
For this reason, a major challenge for the automotive industry is the switch from gasoline-powered to electrically-powered vehicles and decarbonization (reduction of CO2 emissions) as a way to achieve carbon neutrality. YKK AP’s business is still dominated by gasoline-powered vehicles, so there is a need to shift to hybrid vehicles, which we currently work on, as well as other electrically powered vehicles, particularly full EVs. In fact, we are receiving an increasing number of inquiries from automotive manufacturers with whom we do business about aluminum reinforcement materials for use around the battery cases of EVs. However, meeting the demands of such customers often requires rather advanced aluminum extrusion technology, and as such, we are currently actively researching and developing new technologies, including the development of elemental technologies for multi-void(*4) profiles. The issues we are tackling have changed dramatically from the past, and there is a sense of urgency in terms of the need for advanced aluminum extrusion and processing technologies, without which we will not be able to contribute at all to the future of the automotive industry and the realization of carbon neutrality. To further advance our efforts, we established a dedicated contact point for the Aluminum Profile Business at manufacturing plants (manufacturing and technology divisions) and changed the structure to allow for close collaboration between the manufacturing/technology divisions and sales divisions. Our manufacturing, technology, and sales divisions are now working more closely together than ever before, and we are currently working on numerous prototypes.

The image is for illustrative purposes only.
We are also putting our efforts into reducing CO2 emissions during manufacturing. Specifically, we are actively promoting the use of market-obtained recycled materials. The use of market-obtained recycled materials can significantly reduce CO2 emissions in manufacturing compared to the use of new aluminum ingots (new non-recycled aluminum) (*5).
In fact, we have received requests from our customers for new aluminum ingots to be limited to half of the materials used in manufacturing, with the remainder being market-obtained recycled materials. Many of our customers have expressed interest in this recycled aluminum, and we have suggested to interested customers that they join us in using it. In this way, we have developed a full awareness of the importance of environmental considerations today.
Future Challenges in the Automotive and Aluminum Profile Industries
As the world shifts toward a more sustainable society, it is expected that demand for lighter aluminum products and recycled aluminum will increase. In the transportation field, we will firmly capture the demand for lightweight products, especially for EVs, and use aluminum profile components to realize a sustainable society. At present, EV battery cases are very heavy, but since it is difficult to reduce the weight of the battery part right now, we are developing technologies with a focus on how to make the surrounding reinforcement materials and other components lighter. Subsequently, perhaps, driving automation will progress and reinforcement materials will no longer be needed, so we also need to consider what kind of components will be needed at that time.
In addition, because recycled aluminum is a material that can greatly contribute to the reduction of CO2 emissions, we would like to first ensure that it can be used in the areas where we are currently doing business. Eventually, we hope to develop and meet a wide range of demand without limiting ourselves to certain fields.
Realizing these goals also requires organizational development of the Aluminum Profile Department. In order to further strengthen collaboration between the manufacturing/technology and sales divisions, we intend to promote greater personnel exchanges between the various divisions than ever before. As part of these efforts we will, for example, transfer personnel between departments to strengthen collaboration by developing human resources with a deeper understanding of various departments.
In terms of human resource development, we have established a project team of young employees to develop new demand and conduct analysis of the current situation. Then, to ensure that their recommendations are reflected in our business strategy, we hold regular report meetings for our manufacturing plants. In addition, we are conscious of the need for a "broad perspective" that allows us to adapt quickly to the ever-changing trends in the world. To this end we will focus on recruitment activities and increase the number of new graduates, both men and women.
Through these efforts, we hope to strengthen our business, expand existing areas and take on the challenge of new areas, and imprint the YKK AP name firmly in a variety of fields.
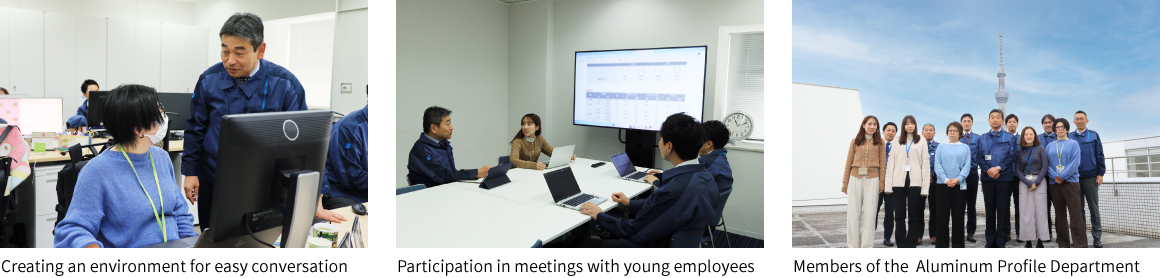
*1: An aluminum alloy made by adding mainly magnesium (Mg) and silicon (Si) to provide improved strength over pure aluminum.
*2: An analysis technique used to determine if a product has any performance problems during the design phase.
*3: Any vehicle that uses electricity for power. This includes various types of vehicles, such as electric vehicles (EVs), fuel cell vehicles, hybrid vehicles, and plug-in hybrid vehicles.
*4: A processing method for extruding aluminum profiles with multiple spaces inside.
*5: Large amounts of energy are used during the process of refining aluminum from an ore called bauxite, which results in high CO2 emissions. However, if recycled aluminum such as market-obtained recycled materials are used, CO2 emissions are only about 3% of those involved in making new aluminum ingots from bauxite. Related content: Toward Achieving Carbon Neutrality: Taking on the Challenge of 100% Aluminum Recycling by a Window Manufacturer

Takeshi Teraki
Teraki joined YKK in 1997. He was engaged in the development of newly developed alloys by conducting development and testing of aluminum profiles and mass production prototypes, and developed prototype components for automobile manufacturers, leading to the start of mass production and delivery in 1999. In 2005, he was transferred to YKK AP AMERICA, and after returning to Japan, he worked as a sales representative for automobile manufacturers before assuming his current position in 2024.
Share this article
- SNS Link X X Share
- SNS Link Facebook Facebook Share
- SNS Link LinkedIn LinkedIn Share
- SNS Link LINE LINE Share
- Copy Link Copy Link Copy Link Copied Link
Related stories
-
Toward Achieving Carbon Neutrality: Taking on the Challenge of 100% Aluminum Recycling by a Window Manufacturer
- Technology
- Manufacturing
- Environment
- Sustainability
-
Stop the Landfill Disposal of Used Vinyl Windows! Disseminating Vision for Vinyl Window Recycling Through Industry-Government-Academia Collaboration, and Taking on the Challenge of "Window-to-Window" Recycling
- Technology
- Manufacturing
- Environment
- Solving Social Issues
-
The installation training network began as a challenge to solve the shortage of sash and curtain wall installation technicians. Taking on challenges in collaboration with partners, and going from Japan to overseas
- Technology
- Installation
- Solving Social Issues
- Story of Project