
Toward Achieving Carbon Neutrality: Taking on the Challenge of 100% Aluminum Recycling by a Window Manufacturer
"We Build a Better Society Through Architectural Products." This is YKK AP’s Purpose and the meaning of our existence—helping to make society better as we conduct our business activities. To achieve carbon neutrality, one of the priority issues for doing so, we are accelerating our efforts to recycle aluminum, a material used in our products. We would like to introduce the significance of those efforts, the challenges we face, and our initiatives.
Aluminum Recycling Which Contributes to Carbon Neutrality
Aluminum is a lightweight, rust-resistant material used for various YKK AP products, which include windows, curtain walls, and exterior products such as carports and fences. At the point when it is refined from an ore called bauxite, aluminum uses large amounts of energy. In terms of CO2 emissions across the entire YKK AP supply chain, material procurement creates the most CO2 emissions, with aluminum accounting for more than 80% of that total (FY2022 results). On the other hand, aluminum is an easily recyclable material, and because it can be recycled by using a small amount of energy, recycling only creates about 3% of the CO2 emitted when making new aluminum ingots (new ingots) from bauxite. Promoting aluminum recycling will lead to a significant reduction in CO2 emissions throughout the supply chain, and will make a significant contribution to achieving carbon neutrality.
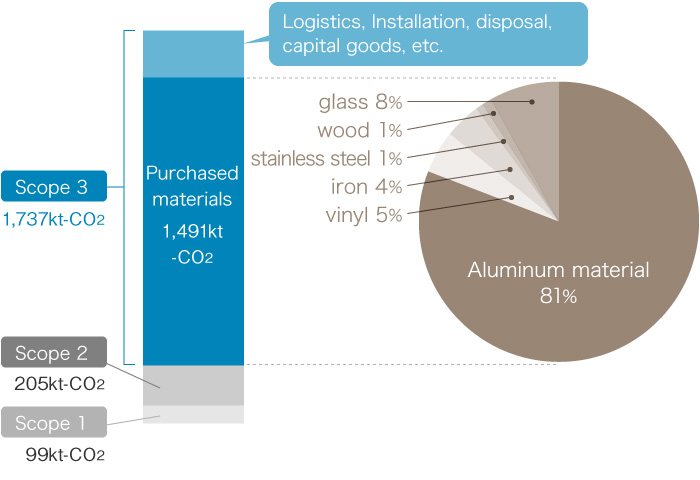
Breakdown of CO2 emissions by YKK AP (FY2022)
Aluminum recycling can be broadly divided into two methods. One method is internal recycling, in which scraps (return scraps) generated by the in-house manufacturing process are reused as materials. The other is external recycling, utilizing market-obtained recycled materials, such as used aluminum sashes and tire wheels. YKK AP has already achieved 100% internal recycling, and we are currently working to increase the external recycling rate. The goal set forth in the "Evolution 2030" Vision, which was announced in March 2023, is a 100% external recycling rate by FY2030. If this goal is achieved, we expect CO2 emissions (Scope 1+2 and Scope 3) in FY2030 to be reduced by approximately 40% compared to FY2013. However, the external recycling rate in FY2022 was 27%. We would like to introduce the efforts YKK AP is making to achieve this lofty goal.
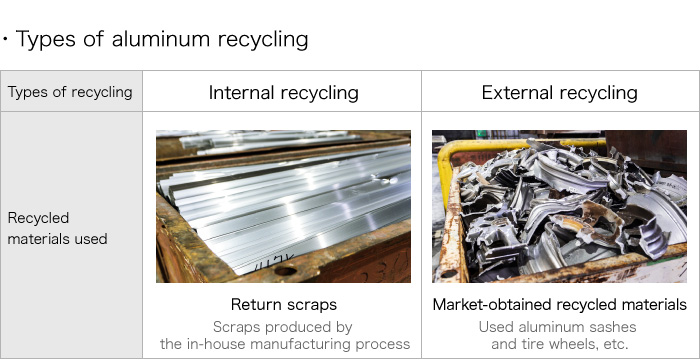
Restructuring Aluminum Casting Facilities for Accelerated Use of Market-Obtained Recycled Materials
The aluminum material used in YKK AP products is made by taking certain amounts of metals, such as magnesium and silicon, and mixing them with externally purchased aluminum ingots, then melting them together in a melting furnace. The material is hardened into "billets," which are then extruded through a die to form aluminum bar profiles. After surface treatment to make the aluminum rust-resistant, the profiles are cut and processed according to the product, then assembled into curtain walls, carports, and other products.
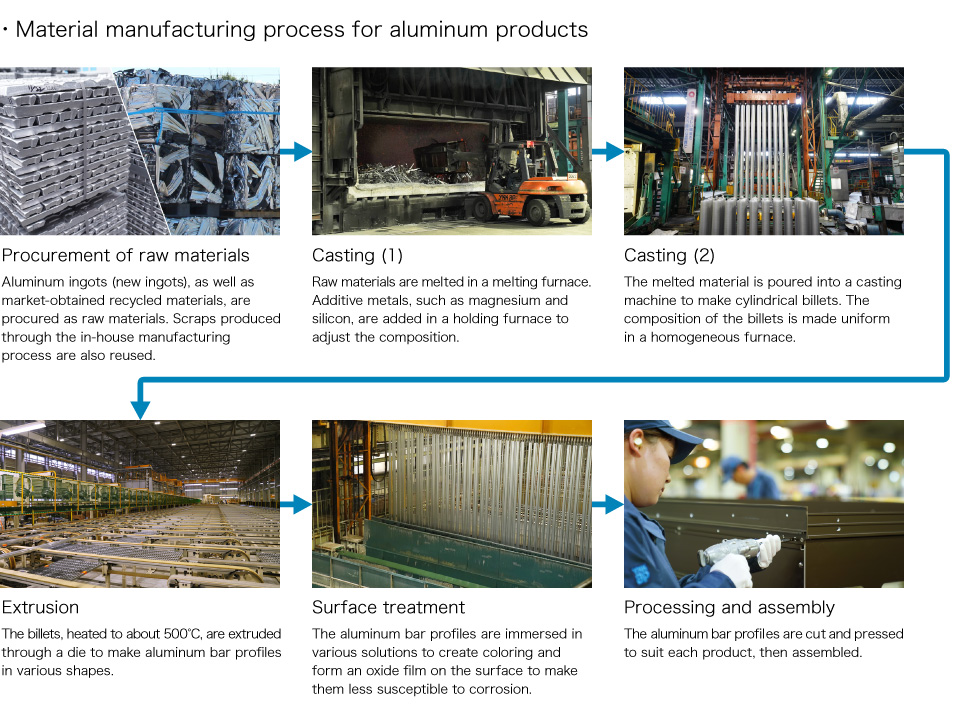
In order to increase the loading ratio of market-obtained recycled materials, YKK AP is promoting the introduction of "recycling furnaces" during casting, which is the process of melting raw materials such as aluminum ingots. While standard melting furnaces can melt large quantities of materials by heating them with a burner, some market-obtained recycled materials, which have different compositions and profiles, are prone to oxidation and increased aluminum depletion when fed into standard melting furnaces. This issue is solved by recycling furnaces. A recycling furnace uses a different method from that of a normal melting furnace to melt aluminum, while reducing the losses caused by increased aluminum depletion. By combining these recycling furnaces with melting furnaces, it is possible to increase the external recycling rate while ensuring a certain level of quality.
Introducing the First YKK AP Recycling Furnace at the Shikoku Plant
As the first step of that initiative, the Shikoku Plant (Kagawa Prefecture) began restructuring its aluminum casting facilities in October 2021. Following the renewal of the aluminum melting and holding furnaces in the first phase of construction, YKK AP's first recycling furnace was introduced in the second phase of construction, and began operation in September 2023.
In truth, there were an abundance of issues to be addressed during the actual installation and operation of the equipment. Koji Hayashi, the General Manager of the Casting Technology Office, Profile Technology Department, who was in charge of equipment installation, said that "Although we had conducted tests prior to the introduction of the furnace, we discovered some issues that we had not anticipated when we started operating it at a practical scale for a long period of time. We are on track for continuous operation, and will work to further optimize conditions." Another major issue that needs to be addressed on-site is the problem of "storage space." Market-obtained recycled materials have three to four times the volume of new ingots, and in some cases, eight times the volume. Aki Taoka, Casting Line Manager of the Materials Production Department at the Shikoku Plant, who is in charge of the aluminum casting process, said that "Because of their large volume, we cannot stock large quantities. We need to procure materials in accordance with production plans, and we are also paying attention to truck dispatch. In addition, we are working on automating the material loading process, since the number of times materials are handled for loading into the recycling furnace will increase," as YKK AP works to address the unique challenges posed by market-obtained recycled materials.
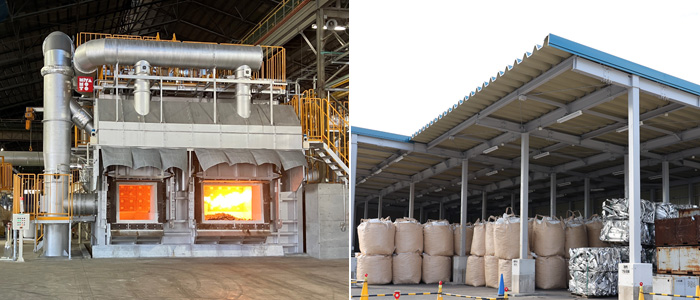
(Left) Recycling furnace (automatic material feeder at the back left)
(Right) Storage space
With the recycling furnace that started operation in September, the Shikoku Plant’s external recycling rate increased from 33% in FY2022 to 50% in December 2023 as a single month. The goal is to achieve a rate of 76% by FY2024 and a rate of 100% by FY2030. In addition, with the Shikoku Plant as the starting point, we intend to restructure and introduce recycling furnaces at all of YKK AP’s locations in Japan with aluminum casting facilities, starting with the Kurobe Plant (Toyama Prefecture), Tohoku Plant (Miyagi Prefecture), and Kyushu Plant (Kumamoto Prefecture). On the other hand, Mr. Hayashi said, "Even now, we can achieve a 100% external recycling rate for specific lots. However, there are many technological challenges involved in achieving a 100% recycling rate for all lots." Bringing the challenges into view, he noted the need to remove impurities during the melting process, and move forward with quality assurance initiatives.
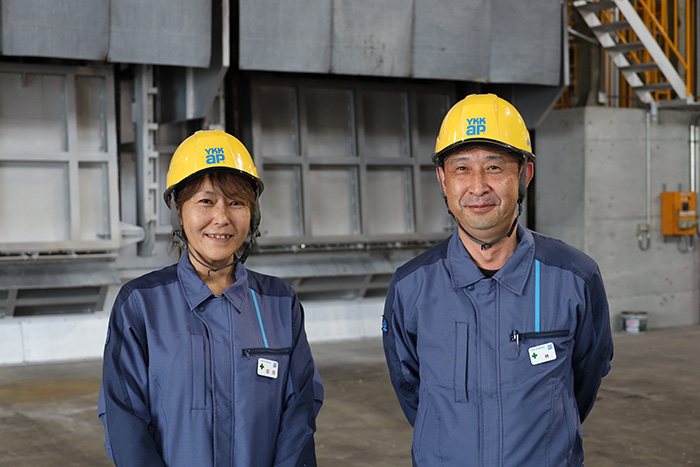
(Left) Ms. Taoka, Casting Line Manager at the Shikoku Plant
(Right) Mr. Hayashi, General Manager of the Casting Technology Office at the Profile Technology Department
Developing Technology to Achieve a 100% External Recycling Rate
In order to address these technological challenges, YKK AP is moving forward with "Creation of a Toyama Resource Recycling Society Model (*1)," an industry-academia fusion hub concept project promoted by the University of Toyama. The aluminum industry is one of the key players in Toyama Prefecture. The purpose of the project is to utilize that advantage to contribute to the revitalization of the local economy and enriched lifestyles by implementing 100% aluminum resource recycling. YKK AP is involved as a secretariat company among the many participating universities, local governments, and companies.
At present, YKK AP is focusing on the following research topics: "creating upgraded recycling technology (*2) to remove impurities," "establishing a production process for recycled aluminum (*3) by sorting market-obtained recycled materials," and "building a recycling system by reducing aluminum oxide and putting it to use." For example, procurement is one of the major challenges in external recycling. Until now, we have used market-obtained recycled materials which have clear origins and identifiable compositions of the original aluminum material. However, as external recycling intensifies, the price of market-obtained recycled materials has soared. It has become impossible to cover production volume simply by using market-obtained recycled materials that have clear origins and compositions. As a result, it is necessary to utilize mixed metals (*4), which do not have clear origins and compositions. Various technological developments are required, including technologies for analyzing these materials, separating them, and removing the impurities produced when mixed metals are melted. Regarding the purpose of YKK AP’s participation in this project, Hiroyuki Tanihata of the Technology Planning Office at the Profile Technology Department, serving as the secretariat for the project at YKK AP, said, "It is difficult for us at YKK AP to pursue these technological developments on our own. We hope that this project will serve as a space where we can gain a plethora of knowledge from industry, government, academia, and the private sector."
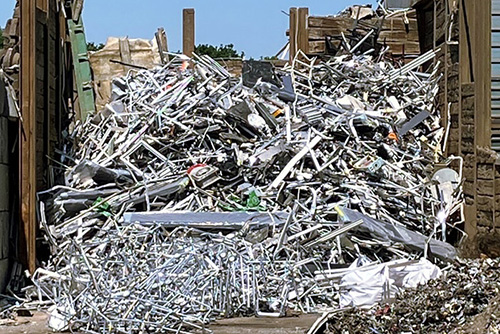
Mixed metals
The plan is for seven engineers from YKK AP to participate in the various research themes being pursued in this project, promoting research and development on shared issues with universities and other companies. YKK AP will also establish a laboratory in Collaborative Research Building for Light Metals, University of Toyama, which opened in October 2023, to further accelerate technological innovation.

The engineers who will participate in the research themes, together with the secretariat; Mr. Tanihata of the Technology Planning Office at the Profile Technology Department is in the back row, second from right
The Future YKK AP is Aiming For
While aluminum recycling is currently garnering attention as an initiative that contributes to carbon neutrality, YKK AP has engaged in internal recycling since we began our architectural products business in 1959. Furthermore, in recent years, we have actively engaged in external recycling, as well. Currently, market-obtained recycled materials may be more costly than new ingots. However, from the perspective of reducing CO2 emissions and from the perspective of the circular economy, we have indicated our policy at YKK AP of using market-obtained recycled materials. One of the reasons for doing so is the outflow of market-obtained recycled materials to places outside Japan. In Japan, aluminum sashes have been supplied to the market in large quantities, and there are many aluminum sashes available in the market. However, many aluminum sashes that become recycling materials after disposal are exported overseas.
Regarding this situation, Mr. Hiroshi Abe, Director and Executive Vice President in charge of Manufacturing, as well as the Head of the Manufacturing Division, said, "We have always been committed to monozukuri that produces goods with local roots for local consumption. Though we are importing new aluminum ingots from overseas, we are working to establish schemes to procure recycling materials from the market—a valuable domestic resource—in a stable way, so that we can utilize them for manufacturing in Japan. Internationally, on the other hand, since there are differences in procurement methods and the performance and functions required for products in each country/region, we have to take measures tailored to each place. For example, in the U.S.A., we are promoting the procurement of green aluminum, which utilizes green energy at the stage of refining aluminum from bauxite, while we are also accelerating our initiatives in China, Indonesia, and India, which are tailored to each country and region."
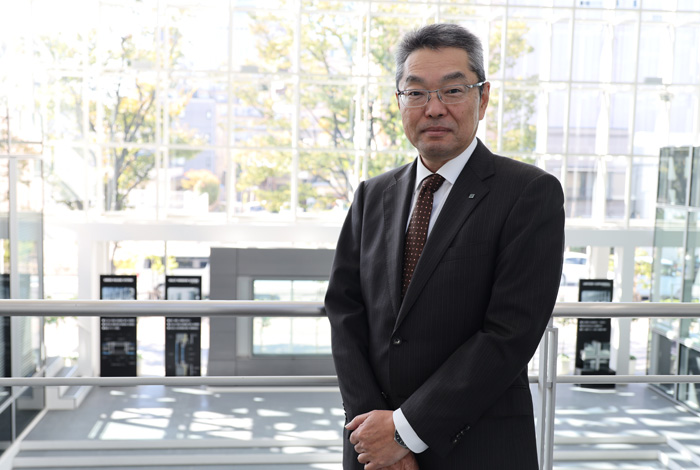
Regarding what YKK AP aspires to be, Mr. Abe said, "The mission of a manufacturer is to provide products that are easy to use and helpful for users. Therefore, I feel that simply saying that we are doing something good for society, such as recycling or significantly reducing CO2 emissions from procurement to manufacturing, is not appealing enough. How can we guarantee user benefits? We need to reduce costs and improve performance and functionality through procurement schemes and technological development." At YKK AP, we are promoting a variety of measures to make it so that aluminum recycling is not merely a method to solve challenges faced by society, such as carbon neutrality and the realization of a circular economy, but also regarded as a strategy to achieve sustainable business growth.
The goal is not aluminum recycling itself, but the provision of better products for society and users through aluminum recycling. Going forward, YKK AP will continue to work on value creation backed by technology, while envisioning the company we want to become.
*1: Industry-academia-government-private co-creation hub site for the creation of a circular economy in Toyama: https://kyoso.ctg.u-toyama.ac.jp/ (in Japanese only)
*2: Upgraded recycling technology: Technology that removes impurities from market-obtained recycled materials to enable higher-quality recycling.
*3: Recycled aluminum: Aluminum ingots made from recycled materials
*4: Mixed metals: Scrap materials that are a combination of multiple metals with unclear origins and compositions. Sorting and component analysis are required to utilize them for recycling.
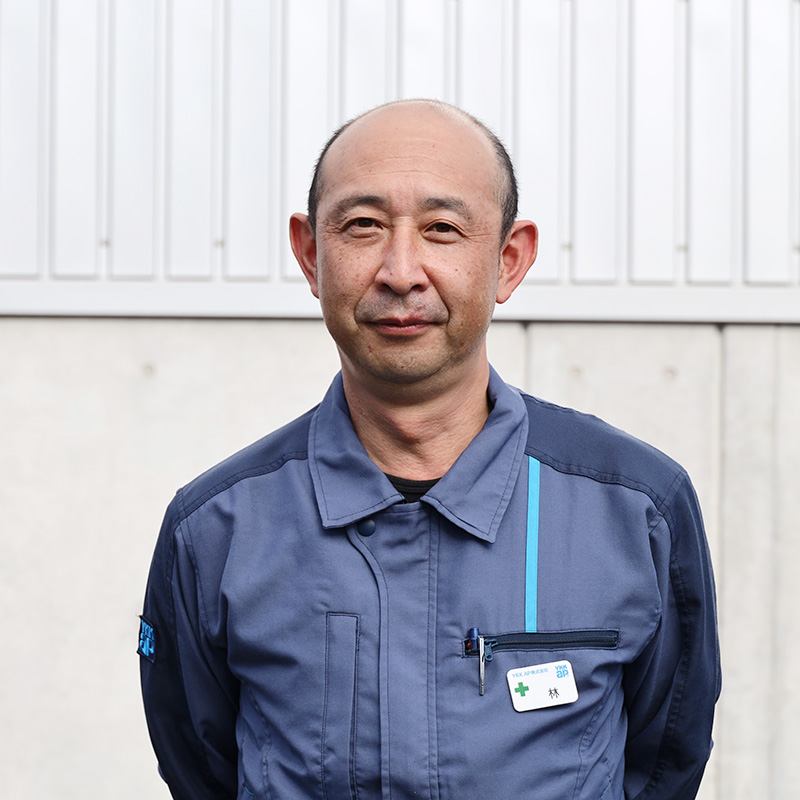
Koji Hayashi
Joined the company in 1986. As the leader of projects to restructure casting facilities, has been involved in the restructuring of various locations, starting with Shikoku. With a foundation in material production, he has extensive experience in equipment installation, including equipment maintenance and serving as line supervisor, as well as the startup of new overseas plants.
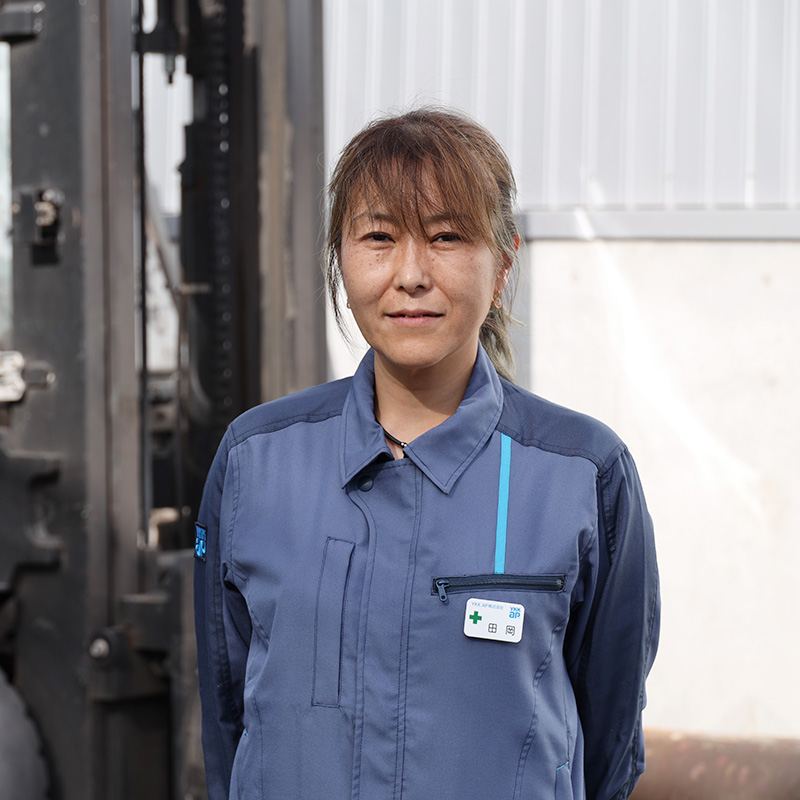
Aki Taoka
Joined the company in 1990. After working in production control and administrative duties on the casting line, she took charge of materials procurement, and since FY2020, she has served as manager on the casting line, which is staffed mainly by young employees with an average age of 31 years old. She is the first female line manager at the Shikoku Plant.
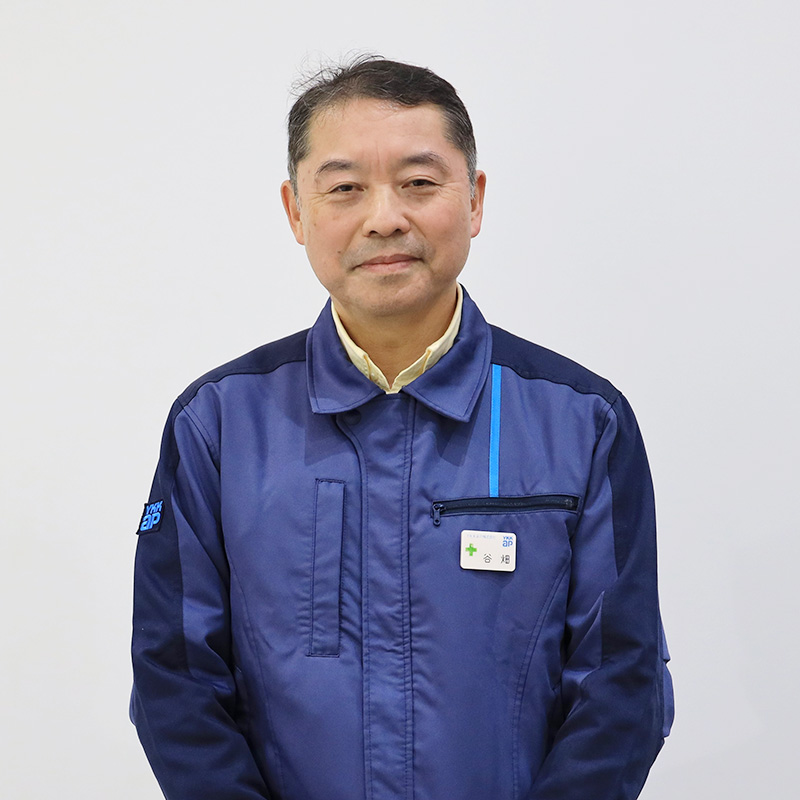
Hiroyuki Tanihata
Joined the company in 1988. As an engineer in material production, he worked on technological development and quality improvement for materials, especially aluminum. In parallel with his work, he obtained a doctorate in engineering. He is also involved in the development of the industry as a director of the Japan Institute of Light Metals and as the YKK AP secretariat for the "Creation of a Toyama Resource Recycling Society Model" project.
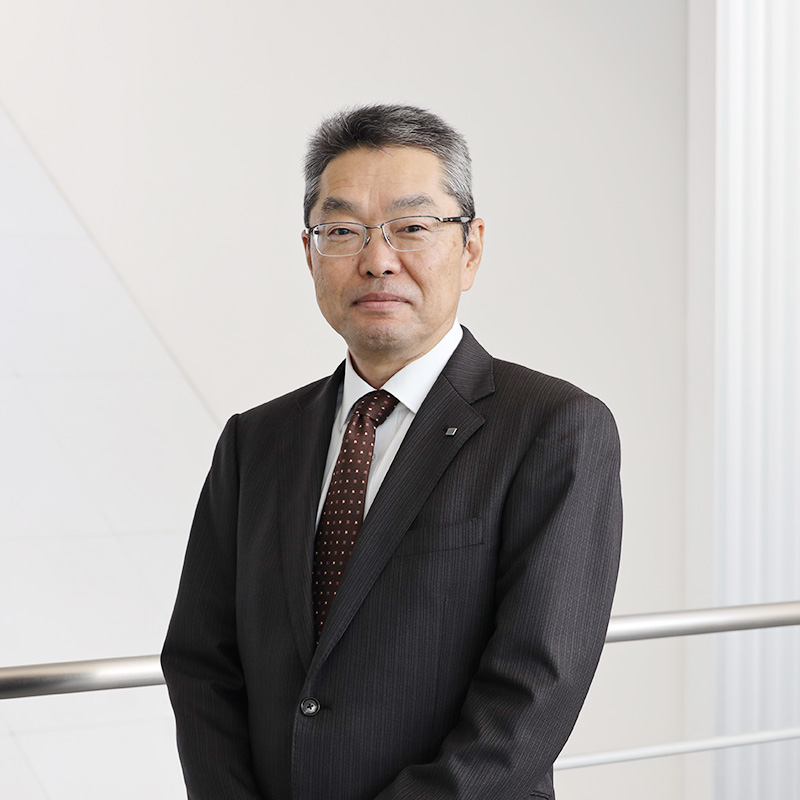
Hiroshi Abe
Joined the company in 1985. After working in fields such as manufacturing technology, he was in charge of setting up the Saitama Mado (Window) Plant and became the plant’s first manager. After serving as the Vice President of the Kyushu Plant and of the Kurobe Plant, he assumed the role of Senior Vice President of the Manufacturing Division in 2021, then became Executive Vice President in charge of Manufacturing from 2022, before taking on the concurrent post of Director starting in 2023.
Share this article
- SNS Link X X Share
- SNS Link Facebook Facebook Share
- SNS Link LinkedIn LinkedIn Share
- SNS Link LINE LINE Share
- Copy Link Copy Link Copy Link Copied Link
Related stories
-
The Evolution of the Aluminum Profile Department into the Automotive Industry’s Manufacturer of Choice
- Aluminum Profile
- Technology
- Sustainability
- Solving Social Issues
-
Stop the Landfill Disposal of Used Vinyl Windows! Disseminating Vision for Vinyl Window Recycling Through Industry-Government-Academia Collaboration, and Taking on the Challenge of "Window-to-Window" Recycling
- Technology
- Manufacturing
- Environment
- Solving Social Issues
-
The installation training network began as a challenge to solve the shortage of sash and curtain wall installation technicians. Taking on challenges in collaboration with partners, and going from Japan to overseas
- Technology
- Installation
- Solving Social Issues
- Story of Project