
Two Breakthrough Technologies for Zero Water Leakage from Windows, Developed by YKK AP—Thoughts Behind the Development of the “W PROOF JOINT” and “Screw Hole Protrusion Processing”
At YKK AP, we have put forward "We Build a Better Society Through Architectural Products." as our Purpose. Our mission is to contribute to society through our products, and we are constantly striving to develop products with a focus on quality. We would like to report on our initiatives for technology development and quality assurance, with the aim of achieving zero water leakage defects from windows.
Table of Contents
- The commencement of development on proprietary technology, sparked by water leakage defects
- Creation of the “W Proof Joint,” a water-blocking technology that is not dependent on the skill of the worker
- Building up the evolution of a new sealer and completing an optimized design
- Screw hole protrusion processing that contributes to leakage control
- Toward the development of better products through the evolution of technology
There are three basic performance characteristics for windows: watertight performance, airtight performance, and resistance to wind pressure. If a window does not perform sufficiently in these areas, it cannot fulfill the natural roles required of a window, such as keeping water out of a house and maintaining a pleasant indoor environment. Among these characteristics, we focused on watertight performance for this article. We interviewed Yuya Oyama—who works in the Technical Research Division for the Materials and Manufacturing Process Technology Group, and is in charge of elemental technology development for materials—about two unique breakthrough technologies developed to guarantee quality.
The commencement of development on proprietary technology, sparked by water leakage defects
Approximately a decade ago, windows made by YKK AP suffered from many water leakage defects. When investigating the areas where water had leaked, we discovered that water was leaking from the joints of the window frames. A window frame consists of four parts (the top, bottom, left, and right), assembled with screws. Rubber components (sealers) for waterproofing are sandwiched between the joints at the four corners to keep rainwater out. These sealers are components which form a tight seal between the parts of the sash (window frame) to ensure airtight performance and watertight performance. However, if gaps are created during assembly or installation, they can cause leaks.
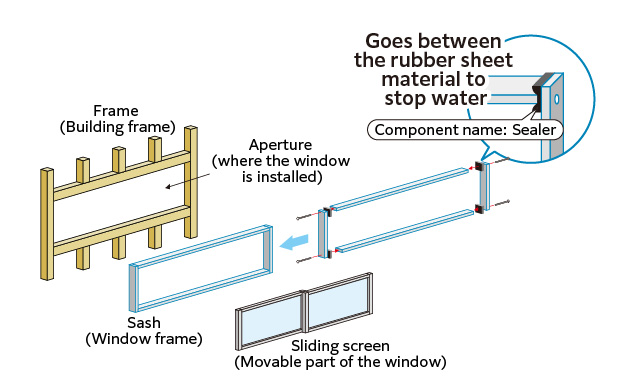
Window construction and sealer installation locations
Generally, the process of installing a window in a house involves the parts of the sash delivered from the manufacturing company (manufacturer), assembled as a window by an assembly company, and finally installed in a house aperture by an installation company. However, at that time, there was a question that could not be fully explained. No matter how many times we repeated internal verification tests, we were unable to replicate the leakages from the window frame. Upon investigating the situations at the window assembly site and during the window installation after assembly, it was surmised that the leakage was due to the creation of gaps at the window frame joints, caused by handling during transportation after assembly and variations in installation accuracy, and that the sealer was not properly performing its water blocking function. We had to develop water blocking technology which takes into account the variability of work during window transport and at the installation site. With this in mind, the development of a new sealer began.
Creation of the “W Proof Joint,” a water-blocking technology that is not dependent on the skill of the worker
While we began testing every conceivable idea each day to realize "leak-proof technology," we could not find a realistic means of achieving this goal. At that time, we noticed that there was a certain technology which had already been put to general practical use. That technology was a material called SAP (Super Absorbent Polymer), which is used in the field of civil engineering for waterproofing structures such as tunnels and bridges. Simply put, it is a highly water-absorbent resin material that swells when exposed to moisture. We thought that we could combine this material with a sealer to seal gaps tightly and prevent leakages when it rains.
If we could bring this idea to fruition, it would be possible to make a sealer which could stop water by swelling in response to rainwater, even if a window were to be installed with gaps in the window frame, while window assembly and installation by workers would remain unchanged. After focusing on this material, we considered how we could incorporate SAP material into our existing sealers. Through a series of prototypes, we sought to put it to practical use.
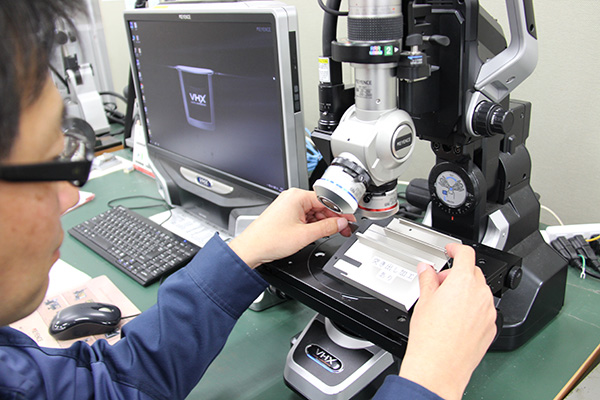
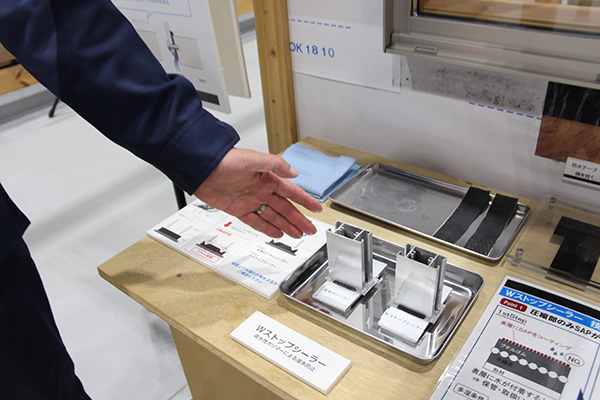
Building up the evolution of a new sealer and completing an optimized design
For the initial design, we proceeded by coating the surface layer of the sealer with SAP material. In terms of results, although the design was very effective at preventing leaks, issues with durability stood out, such as the fact that the surface layer of SAP material would stream out every time it rained. It was also extremely expensive. Therefore, after repeated verification and improvement, we changed the design to knead the SAP material into the sealer. Taking this approach allowed the SAP material to react and swell only where it was compressed by the window frame parts, resulting in a structure that could continue to guarantee long-term performance while also reducing costs. Based on this design, a revised specification for the hardness of the rubber—the primary material used in the sealer—was reviewed to ensure that the sealer would provide adequate water blocking performance, and this led to an optimal solution, which has been used to this day.
With the addition of a new element to a conventional sealer to seal gaps through the expansion of SAP material, we named the new sealer, which demonstrates a W (double) water-blocking function, "W Proof Joint."
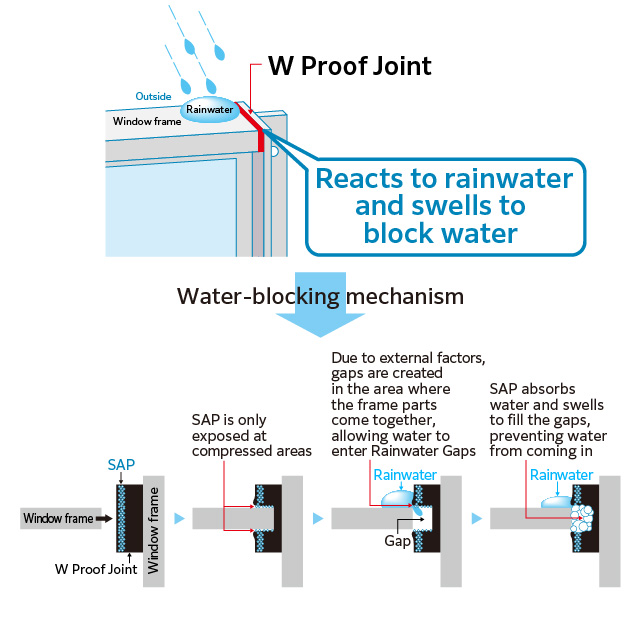
W Proof Joint's unique water absorption and swelling mechanism (water-blocking mechanism)
Screw hole protrusion processing that contributes to leakage control
Although the development of the W Proof Joint dramatically reduced the number of leakage defects, the actual number of occurrences did not reach zero. We found that leaks were still occurring in windows where this sealer was used. In order to identify the cause of this issue, we visited sites across Japan where defects had occurred to investigate and verify the working environment and conditions during installation.
Investigation of the factors causing the window to leak revealed that the sealer had been compressed by strong forces and damaged by friction. This raised the possibility of a problem in adjusting the force with which the worker tightens the screws when assembling the window. Applying too much force will damage the sealer due to friction, while too little force will cause the sealer to not be sufficiently crimped, which causes gaps. Even the best sealer will not be fully effective in keeping water out if it is damaged, or if there are gaps which are bigger than expected.
We therefore thought about developing a technology which would appropriately control the screw tightening force, without being dependent on the skill of the worker, and came up with the idea of forming a protruding shape on the periphery of the screw hole at the same time as the hole is being drilled. The benefit of this processing technology is that by creating a convex protruding shape on the screw hole section of the window frame, that section clamps down when the screw is tightened, eliminating excessive tightening of the screw by the worker. As a result, the technology reduces the risk of the sealer wearing down or being damaged. This allows for consistent and accurate assembly conditions.
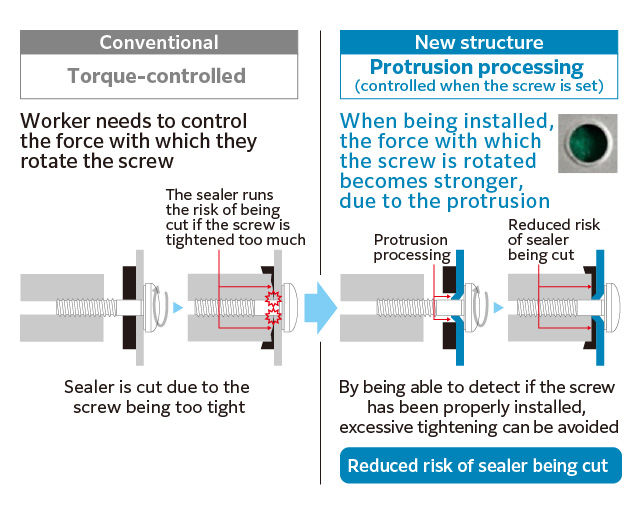
About the Screw Hole Protrusion Processing Technology
By employing this processing technology together with the aforementioned W Proof Joint technology, our products can fully demonstrate their water-blocking performance. The W Proof Joint is now used not only in domestic products, but also in products sold overseas, and is making a significant contribution to reducing leakage defects. We will continue to develop these technologies and apply them for purposes other than frame joints.
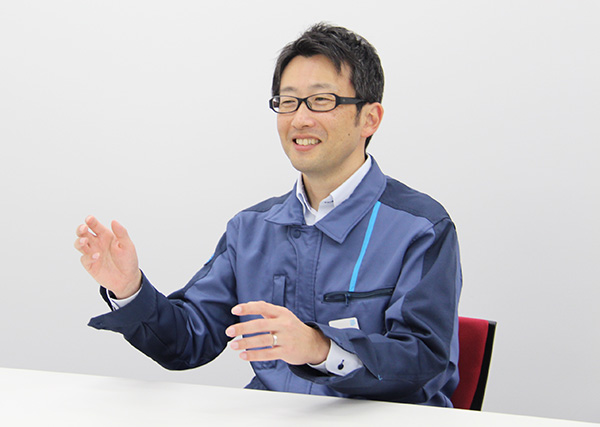
Toward the development of better products through the evolution of technology
The two technologies introduced here are examples of how we have come to realize that technologies that we had been considering independently can be combined to great effect. We must continue to constantly incorporate new ideas and evolve our technology. As an engineer myself, I believe it is important to be interested in a variety of information, to find new ideas and hints for solving problems, and to create new technologies that will lead us in the right direction.
The housing industry is also faced with various issues these days, such as a shortage of sash and curtain wall installation technicians. While coming up with products that eliminate defects is one of our initiatives, we also need to think about ways to make installation easier. We intend to continue our pursuit of technology to create better products, such as making smoother installation a reality, through these efforts.
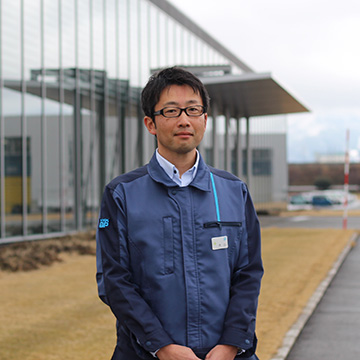
Yuya Oyama
Since joining the company in 2001, has been in charge of elemental technology development pertaining to resin materials.
Obtained his doctorate in 2020 (doing research related to the swelling behavior of rubber material caused by the addition of a water-absorbing polymer)
He has been working hard on research and development, making use of his experience and knowledge.
Share this article
- SNS Link X X Share
- SNS Link Facebook Facebook Share
- SNS Link LinkedIn LinkedIn Share
- SNS Link LINE LINE Share
- Copy Link Copy Link Copy Link Copied Link
Related stories
-
An integrated production system: a commitment to manufacturing that pays attention to even a single screw
- Technology
- Manufacturing
- Story of Development
-
Establishing a digital R&D center in the U.S.A. What is YKK AP's digital strategy for smart factories?
- R&D
- Technology
- Installation
- DX
-
Recreating heavy rain, storms, and other harsh natural environments for verification. “Field verification” initiatives to provide product value through reliable quality and performance evaluation.
- R&D
- Technology
- Solving Social Issues