
Developing sustainable logistics: our efforts as an architectural product manufacturer to solve the 2024 problem and reduce driver working hours
“We Build a Better Society Through Architectural Products.” This is YKK AP’s Purpose and the meaning of our existence as we conduct our business of developing, manufacturing, and selling windows, doors, interior architectural products, exterior products, curtain walls, and other items. This article covers our logistics initiatives for delivering high-quality products to customers.
Circumstances remain harsh in the logistics industry, including the driver shortage, increasing age of drivers, problems of long working hours and low wages, environmental issues, and a sudden increase in home delivery. We are also less than one year out from the “2024 problem,” when a regulation will apply to the maximum overtime hours for truck drivers. The SCM Department, which is in charge of the supply side of YKK AP’s monozukuri via an integrated production system, is making various efforts for product quality and supply stability. We spoke about the SCM Department’s initiatives with Hiroyuki Yotsuyanagi, head of the Logistics DX Promotion Office in the SCM Department. He works at the Hokuriku DC in Namerikawa City, Toyama Prefecture, which handles the largest distribution volume among our 10 logistics sites in Japan.
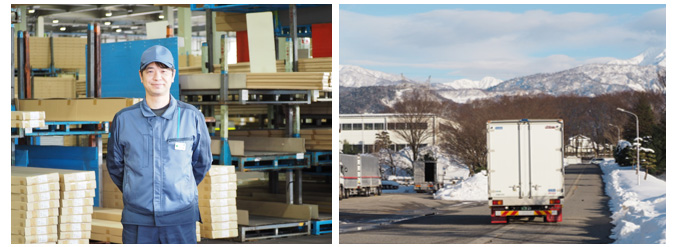
Logistics issues for architectural product manufacturers
Our windows, doors, and other products come in many shapes and sizes. Some are flat, and some are more than five meters long. In contrast, we also ship small packages with just a few screws. Residential architectural products are becoming heavier these days due to better thermal insulation and higher performance. For example, some entrance doors can weigh more than 50 kilograms, and some large triple-glazed windows exceed 100 kilograms. We also have many fragile products made from glass and other materials, posing major difficulties in the logistics process.
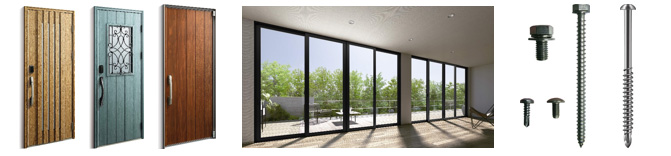
YKK AP has been revising its logistics system while experiencing these challenges inherent to architectural product manufacturers, along with the labor shortage throughout the entire logistics industry. The basis of this is “unit-loading,” an efficient shipping system that consolidates loads into pallets, containers, and other units. We are working to enhance and expand unit-loading and to achieve sustainable logistics.
YKK AP’s unit load system
Switching from direct loading performed by humans
Human workers used to stack products packaged in cardboard boxes directly on truck loading platforms for trunk line transportation. This is called “direct loading.” The drivers stacked the cardboard boxes, which provided good loading efficiency, but it took more time for cargo loading and unloading, resulting in more working hours for drivers. But more than anything, this method was very physically demanding. They had to be able to efficiently stack the cargo, which required advanced skills and intuition. To solve these issues, we switched from direct loading of individually packaged boxes to a system for shipping and storing pallets (single units).
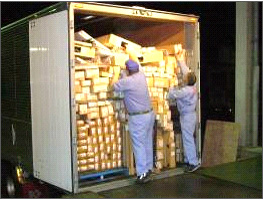
With direct loading, human workers stack products packaged in cardboard boxes directly on truck loading platforms
Developing a new transportation pallet that’s lighter, thinner, and stronger
We began palletization in 2015 and have been loading products on pallets ever since, but they were introduced as efforts at individual sites to improve loading efficiency, rather than as a companywide standard. The SCM Department established a team and worked with specialized business operators to start developing a new pallet. The old type had a thick wooden bottom and steel frame. We fully reviewed the construction, starting from scratch, to successfully create a new type of lightweight, thinner, stronger pallet that is compatible with the old type and easy to operate. The internal volume is 8% larger than before, and the load limit was increased from 400 to 600 kilograms. They can be stacked 10 at a time when returning empty pallets, compared to the previous number of eight. We paid particular attention to empty space at the top of low-floor trucks (*1), which we hadn’t been able to use effectively. By adding ribs to the side boards, we further increased vertical loading space by 25%.
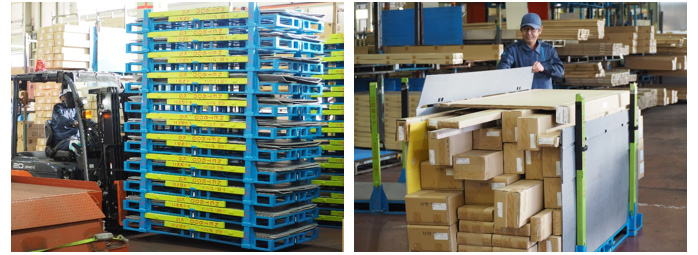
(Left) Stacked empty pallets being moved with a forklift
(Right) Adding side boards to improve vertical loading space
Developing Y-Caps, a new system to optimize product pallets and truck loading
The new pallet holds more cargo, but there was also the issue of how to effectively load pallets on truck loading platforms (called “palletization”). When depending on worker skills to load large quantities of cargo with different sizes and lengths, gaps can be left between boxes depending on how they are stacked. This reduces load size, leads to the unnecessary use of more pallets and trucks, and results in inconsistency. We developed the Y-Caps system to derive optimum methods for combining items. In this new system, each product or pallet is regarded as a single cube. It uses a cubic load optimization theory based on the operations research (OR) method. We solved each issue to bring it into practical use, such as considering the unique cargo characteristics, and reproducing the multi-step palletization process from the production line to the shipping site. With Y-Caps, in the truck assignment phase we can clearly visualize the necessary number of pallets, how they should be loaded, and how many trucks are needed. Moreover, we can focus on empty space and consider adding additional cargo to make more efficient arrangements.
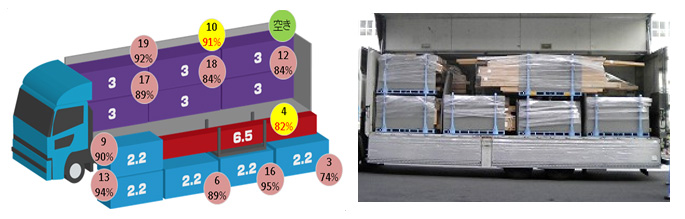
(Left) Diagram of how Y-Caps optimizes pallets and truck loading
(Right) Truck platform loaded according to the diagram
We started full-on palletization (with both tangible and intangible measures) in 2016. Our initial palletization rate of 54% grew to 92% in FY2022.
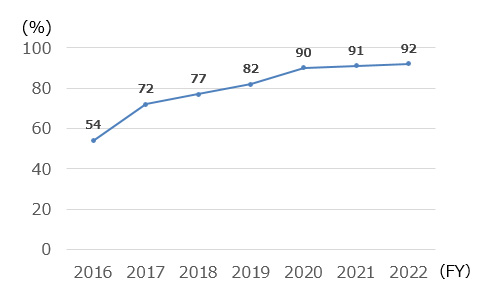
Palletization rate for residential component supply products
Unit-loading reduces the burden on workers and drastically cuts their working hours
Unit-loading makes loading and unloading much easier and quicker than before. Direct loading required two workers who spent three hours loading and three hours unloading, for a total of six hours. Pallets are transported by forklift; it takes just 15 minutes to load cargo and 15 minutes to unload it, for a total of 30 minutes. This is a 5.5-hour reduction for a single process. We’ve also achieved better work efficiency for other processes by using pallets to streamline preparations before loading and sorting after unloading.
As a company that ships products, YKK AP will continue making creative efforts to expand our unit-loading and strive for smart logistics with other business operators in that industry.
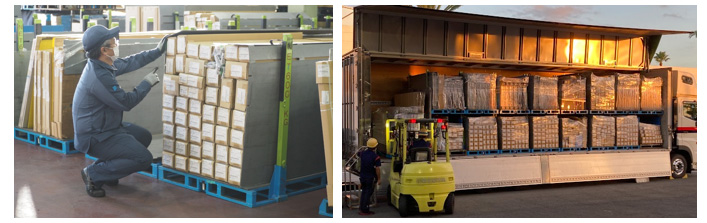
(Left) Confirming products on each pallet in the loading space
(Right) Using a forklift to load pallets on a truck
Working to solve the 2024 problem facing the logistics industry
With the goal of work style reform in the logistic industry, the revised Labor Standards Act that comes into effect in April 2024 sets a maximum of 960 annual overtime hours for truck drivers. In principle, this puts a strict limit on their yearly work hours, from 3,516 (the current average) to 3,300. Although this is expected to improve the working environment for drivers, it will decrease the daily cargo carried by each driver. Some have pointed out the risk that this will worsen the labor shortage and lead to an inability to deliver items. We call this the “2024 problem.” Due to our close ties with logistics, in 2019 we endorsed the “White Logistics” Movement led by the Ministry of Land, Infrastructure, Transport and Tourism, and we have worked to streamline our logistics and boost productivity with the aim of steady, sustainable logistics in and after the year 2024. We are also making efforts to further reduce driver working hours after establishing the unit-loading transportation system.
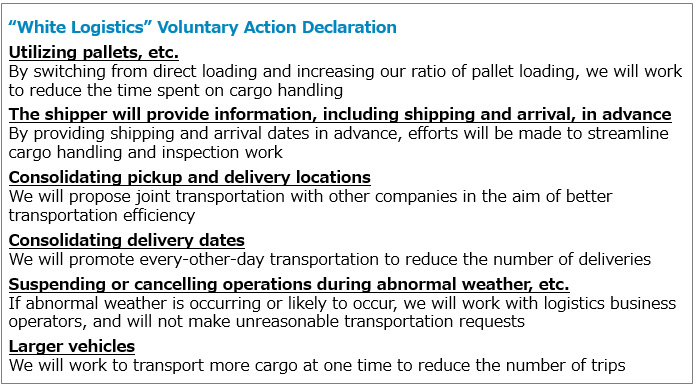
First, we conducted interviews at all logistics sites to understand the current situation: six distribution centers (DCs) and four transfer centers (TCs). We also made a list of routes where drivers had long working hours, then reached out to logistics business operators on these routes and planned improvement measures to be carried out in FY2023, including organizing the transit points.
YKK AP’s logistics and production sites (as of April 2023)
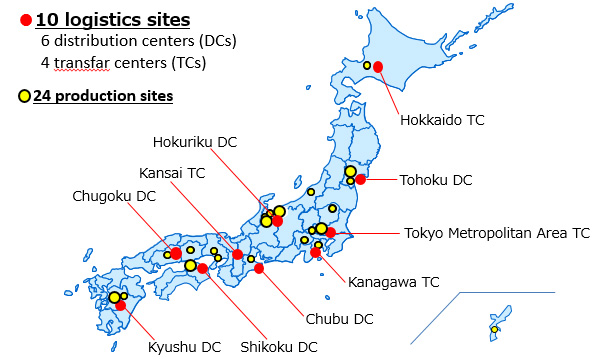
SCM Department meeting
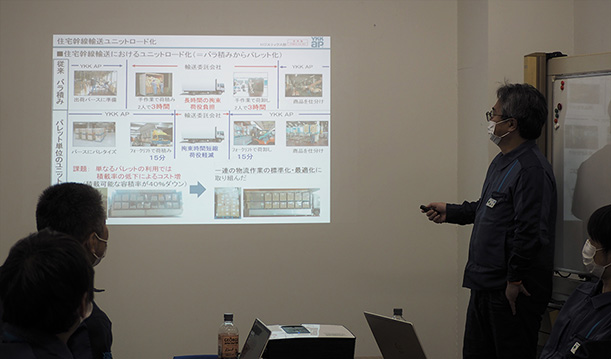
Working for sustainable logistics
Although the logistics industry is facing a range of issues, there are still many things we must do as a shipping company. We are striving for sustainable logistics via initiatives such as building stable supply systems, digital transformation to boost productivity, and joint transportation with other companies. As part of our monozukuri, the SCM Department’s role is to deliver our important products to the sites where they will be installed. Yotsuyanagi said, “Salespeople suggest and sell products, and the manufacturing side produces and supplies them. I want to properly fulfill our supply responsibility by ensuring there are no cases in this process when customers cannot receive our products.” We will cooperate with drivers and transportation businesses and build trust with them in the aim of being a shipping company that is chosen by others.
*1: Trucks with little distance between the ground and loading platform. This makes it easier to load and unload cargo, and lower ground clearance provides a larger cargo space.

Hiroyuki Yotsuyanagi
Joined YKK AP in 1992. Worked in information system planning, development, and operation at the Kurobe Architectural Product Processing Plant and Kurobe Ogyu Plant. Transferred to the SCM Department in 2008. As the leader for rebuilding core logistics systems, he is in charge of planning, building, and promoting these systems. Has worked on logistics digitalization in his current position since 2021.
Share this article
- SNS Link X X Share
- SNS Link Facebook Facebook Share
- SNS Link LinkedIn LinkedIn Share
- SNS Link LINE LINE Share
- Copy Link Copy Link Copy Link Copied Link
Related stories
-
Toward sustainable logistics with Tokyo Metropolitan Area DC, a logistics site that aims to solve the 2024 problem
- Logistics
- Sustainability
- Solving Social Issues
- Story of Project
-
YKK AP and residential businesses team up for housing performance improvement renovation as a way to solve the vacant house issue
- Residential Business
- Sustainability
- Solving Social Issues
- Story of Project
-
The Evolution of the Aluminum Profile Department into the Automotive Industry’s Manufacturer of Choice
- Aluminum Profile
- Technology
- Sustainability
- Solving Social Issues