
YKK AP and residential businesses team up for housing performance improvement renovation as a way to solve the vacant house issue
"We Build a Better Society Through Architectural Products." This is YKK AP’s Purpose and the meaning of our existence as we conduct our business of developing, manufacturing, and selling windows, doors, interior architectural products, exterior products, curtain walls, and other items. As a domestic Residential Business initiative, we are working to promote and popularize housing performance improvement renovation.
Table of Contents
- About the renovation demonstration project for the housing performance improvement
- Renovating the Kyomachi-style Kyoto Daigo House, built 112 years ago
- Expanding performance improvement renovation via communication with business operators
- The good points of housing performance improvement renovation are drawing more attention today
In the renovation demonstration project for the housing performance improvement started in 2017, we perform performance improvement renovation focused on thermal insulation and seismic resistance for existing single-family homes. This project is based on the concept of teaming up with nationwide residential business operators to give old buildings the same or higher value as new construction. We have so far completed 20 projects with 19 business operators in 16 prefectures. These companies do businesses in different ways according to their type, and there are varied requirements for existing housing and local characteristics in each area. We spoke with Takao Nishimiya, head of the Performance Improvement Renovation Promotion Office, Renovation, Residential Business Division, who is in charge of the renovation demonstration project for the housing performance improvement.
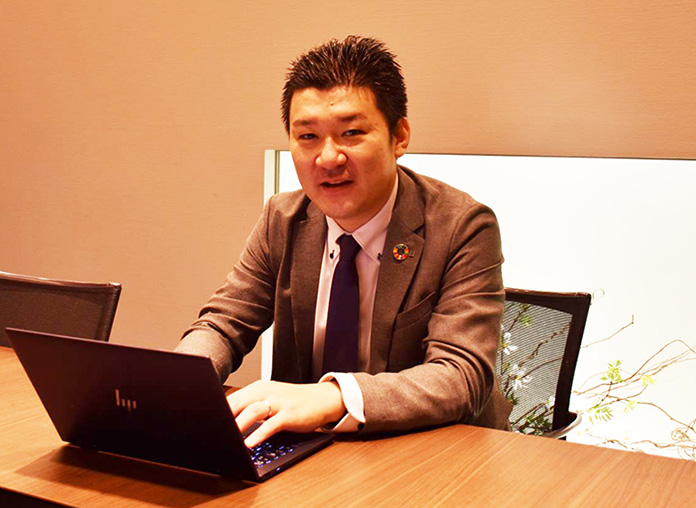
About the renovation demonstration project for the housing performance improvement
In this project, we perform full-scale renovations of the entire home, leaving only structural material like pillars and beams. This means our products are installed on the building frame—just like when putting up a new house—which is totally different from partial renovations, such as replacing a single window. For a new build, window positions are obviously part of the construction process. But with renovation, you have to remove the wall while leaving the framework to install a window. You must consider the existing house’s condition and think about putting thermal insulation material around the window as well. No matter how much manufacturers like YKK AP know about windows, we lack the skills and know-how to install them. That’s why we needed the cooperation of residential business operators to implement this project. The important point of this project is that renovations are done to improve performance for thermal insulation and seismic resistance.

The Kobe Rokko House, completed April 2019 (City of Kobe, Hyogo Prefecture, business operator: KIMURA-GRIT Group)
From left: Before, Demolition, Installing seismic frames, After
Solving issues with performance improvement renovation
Housing stock is said to number roughly 60 million units in Japan, including vacant homes. Performance is an issue: 87% of these homes do not meet the current energy-saving standard for thermal insulation performance, and more than 90% are at risk of collapse (including high risk) due to their seismic performance.
The question is, how do we make sure that these homes remain safe, secure, and comfortable places to live? It’s not difficult to demolish and rebuild a home, but we started this project because we thought it would be possible to create high-performance homes by renovating them with windows and doors that have high thermal insulation and seismic performance. And if we could demonstrate how performance improvement renovation works and promote this initiative, we believed we could help solve a range of social issues facing Japan, for instance by reducing the amount of architectural materials (and waste), cutting CO2 emissions through high thermal insulation, and invigorating local communities by bringing value back to unoccupied homes. This would provide more housing choices to people looking for places to live, and become a new business model for manufacturers. Our goal in this project is to build a better society.
Renovation for thermal insulation and seismic performance
The Building Standards Act and other performance standards apply to new housing, but because there are no clear criteria for renovation, businesses and homeowners decide on the necessary performance. For this project, our standards are Thermal Insulation Performance Level 6 and Seismic Resistance Level 3.
New builds must meet or exceed Thermal Insulation Performance Level 4 in 2025 and Level 5 in 2030. We are aiming for Level 6, which is higher than both of these. Our goal of Seismic Resistance Level 3 means the house will not collapse during an earthquake registering 6 Upper to 7 on the Seismic Intensity Scale. People can continue living in the house, which safeguards their lives and assets. In contrast, Level 1 means the house will not be immediately destroyed, but is at risk of serious damage.
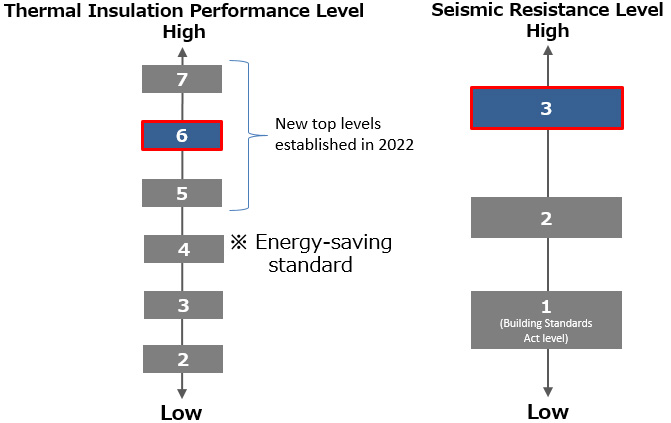
APW 330 high-performance vinyl windows and APW 430 high performance triple-glazed vinyl windows are used to achieve this performance. These products provide roughly four to seven times better thermal insulation than the single-pane, aluminum-framed glass windows in many existing housing stock units. We suggest which to use according to the performance and cost considerations of each project. We provide our Frame II products for seismic resistance at windows and doors. Windows and doors are weak points. We use simulations to suggest how many products should be installed in what locations to retrofit them and reach Level 3, even for large windows and doors.

Renovating the Kyomachi-style Kyoto Daigo House, built 112 years ago
The project came together through a combination of proposals to improve performance based on the products we manufacture, along with on-site installation by local business operators. We worked with Hiroaki Mizushima, head of the Planning Department at HEIANKENZAI Co., Ltd., on the Kyoto Daigo House (completed in November 2019). I talked with him about the significance of this project.
HEIANKENZAI is a residential product trading company that does business in Kyoto. For this renovation, HEIANKENZAI served as the secretariat for the Kyogurashi Network while working together with design offices, contractors, real estate agents, and other companies. HEIANKENZAI has grown its business by renovating Kyomachi-style homes and putting them into circulation with the latest architectural products using skilled techniques, while also preserving the uniquely beautiful, elegant scenery of Kyoto. They heard about the renovation demonstration project for the housing performance improvement from a YKK AP employee. Mizushima said he had not paid much attention to performance before that point, but he could sense the passion in YKK AP’s successive proposals. He got involved in this project because he thought he could learn a lot from it.
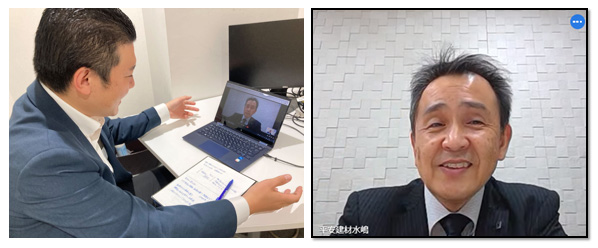
This Kyomachi home was built 112 years ago and is located right across from Daigoji temple, a UNESCO World Heritage Site. We replaced all 14 of the single-pane, aluminum-framed windows with vinyl windows. We also installed thermal insulation in the ceiling, walls, and floors, which had none. The Kyoto Daigo House’s thermal insulation performance is over seven times higher than before the renovation. It’s comfortable while also saving energy, with annual heating and cooling costs roughly 50% lower than before. We used a FRAME II at one location to achieve strength equivalent to Seismic Performance Level 3 without having to cut back on windows or floor space.
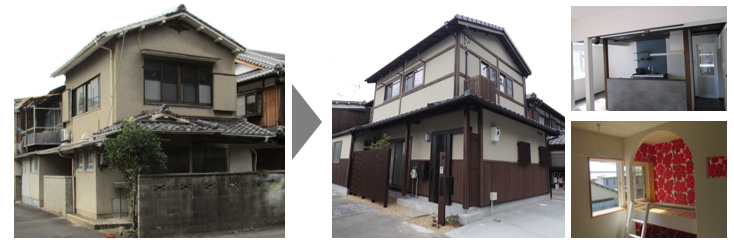
The Kyoto Daigo House, completed November 2019 (Kyoto City, Kyoto Prefecture;
business operator: HEIANKENZAI Co., Ltd. [KYOGURASHI NETWORK])
(Left) Before (Right) After (exterior/interior)
There’s no such thing as too much when it comes to comfort
The completed Kyoto Daigo House serves mainly as a model home for professional users, and is utilized to offer performance improvement renovation expertise and share information with the local community. A cumulative total of 300 professional users have visited, and about 30 regular couples looking for homes have taken tours. Mizushima works with these customers at the house. He said, "I know that performance has been improved when someone who just stepped into the entryway says, ‘Something seems different.’ Even if visitors don’t comprehend the performance levels, numerical values, or other slightly difficult concepts, they can feel whether the inside of the house is warm or cool. I’m glad we are part of this project so we can at least show people that performance improvement renovation is a housing option." He spoke about the significance of the project as follows: "At first I thought it would be too much to use windows with the same performance level as those in Hokkaido. However, I don’t like the phrase ‘too much’ anymore (laughs). Comfort is relative to high specifications—there’s no such thing as too much when it comes to comfort."
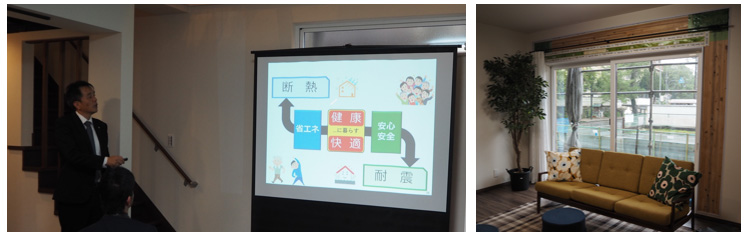
(Left) Mizushima explaining the Kyoto Daigo House concept at the model home
(Right) An installed FRAME II left unfinished for informative purposes
Expanding performance improvement renovation via communication with business operators
This isn’t just a demonstration project—another aim is to teach nationwide business operators about this technical expertise and business model. During construction, we hold tours to showcase things that cannot be seen after the project is completed, such as the state of seismic performance and foundation retrofitting, as well as thermal insulation material and airtight installation methods. When the renovation is complete, we conduct tours to show what the building looks like and share information about the renovation concept. It’s true that this involves revealing our expertise to local businesses in the same industry, but this project is done with cooperation from members who agree with our thinking about performance improvement renovation. These tours have been attended by a total of 3,000 business, and we have communicated and exchanged opinions with them as more people have gotten involved in the project.
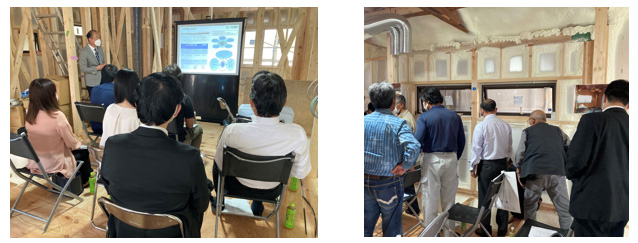
Construction tour at the Minamishinshu Takaha-cho House (Iida City, Nagano Prefecture; business operator: U-Kenchiku Co., Ltd.)
Founding the Association of Performance Improvement Renovation
Through these projects, we have learned it is possible to achieve Thermal Insulation Performance Level 6 and Seismic Performance Level 3 by renovating homes. We’ve also heard from member businesses and tour participants about many different issues, such as how to choose a building and structural problems revealed after demolition. Renovation can be difficult to understand, laborious, and troublesome, creating a bottleneck for people who want to get into this business. We started the Association of Performance Improvement Renovation in October 2021 with the goal of building an environment that facilitates housing performance improvement renovation projects, and of helping promote and popularize this market. We publicize information about the overall workflows and processes, from property selection to transfer. We also offer partner services from specialized companies in each field and various tools and support to handle wide-ranging concerns. Current members include contractors, real estate companies, renovation businesses, and distributors. We created the Association of Performance Improvement Renovation as one way to solve the issues we encountered during projects. I think the next step is making it into a hub not only for communication between members, but also for matching between members, and between members and general customers.
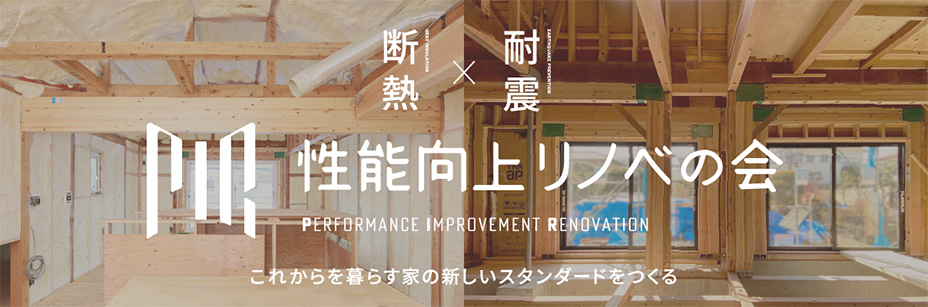
Association of Performance Improvement Renovation website:
https://pireno.ykkap.co.jp/ (in Japanese only)
The good points of housing performance improvement renovation are drawing more attention today
The market and environment have changed significantly during the five years since launching the renovation demonstration project for the housing performance improvement. New lifestyles are being established because of the COVID-19 pandemic, and housing is becoming increasingly diversified. More people are interested in renovation and buying used homes. A recent problem is the rising cost of new housing caused by soaring material prices. Renovation is drawing attention because it can be more affordable by reducing the amount of wood used and utilizing existing parts such as pillars, beams, and foundations. And with increasing electricity costs for heating and cooling, performance improvement renovation is a way to save as much or more energy compared to a new house.
Promoting performance improvement renovation
As performance improvement renovation gains increasing significance in society, we must continue promoting it to business operators while stepping up our efforts to convey more of its good points to individuals looking for a place to live. Nishimiya enthusiastically stated, "Even with renovation, we must tell customers what kinds of lifestyles these products can provide, and how they can fulfill their home-related hopes and resolve their concerns. I want to provide more opportunities like the demonstration project for them to experience this performance, and to continue working with businesses to promote performance improvement renovation."
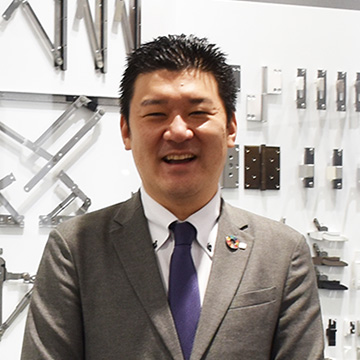
Takao Nishimiya
Joined YKK AP in 2008. Worked in sales for major housing manufacturers and builders before transferring to the Performance Improvement Renovation Promotion Office, Renovation, Residential Business Division in 2020.
Founded the Association of Performance Improvement Renovation in October 2010, where he is in charge of planning and managing the overall performance improvement renovation business.
Share this article
- SNS Link X X Share
- SNS Link Facebook Facebook Share
- SNS Link LinkedIn LinkedIn Share
- SNS Link LINE LINE Share
- Copy Link Copy Link Copy Link Copied Link
Related stories
-
Toward sustainable logistics with Tokyo Metropolitan Area DC, a logistics site that aims to solve the 2024 problem
- Logistics
- Sustainability
- Solving Social Issues
- Story of Project
-
Developing sustainable logistics: our efforts as an architectural product manufacturer to solve the 2024 problem and reduce driver working hours
- Logistics
- Sustainability
- Solving Social Issues
- Story of Project
-
Creating warm houses that don't rely on heating and cooling. The reason YKK AP is working to popularize energy-efficient “vinyl windows” with high thermal insulation.
- Residential Business
- Solving Social Issues
- Story of Project