- HOME
- Sustainability
- Monozukuri and the Value Chain
- Manufacturing and Logistics
Manufacturing and Logistics
Monozukuri and the Value Chain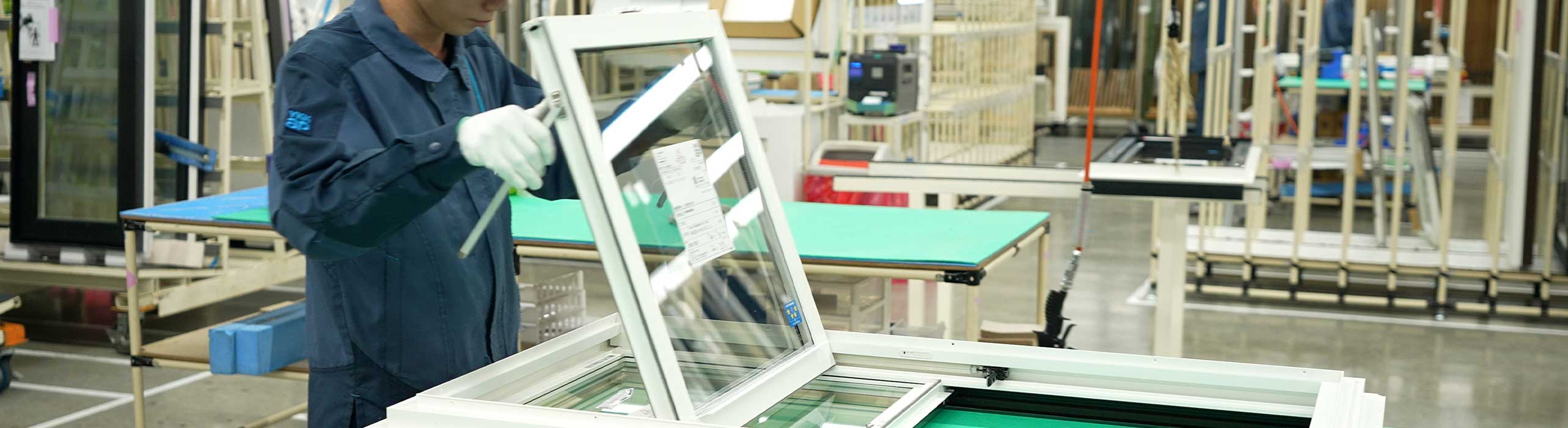
Integrated Production System
YKK AP is committed to an "integrated production system," in which the company itself handles everything from materials, components, and production equipment to processing and assembly. Our insistence on such a system enables us to develop technology quickly, control costs throughout the supply chain, and guarantee reliable quality.
In addition, all manufacturing processes are carried out at YKK AP's domestic and overseas manufacturing sites. This includes processing the glass used for our mainstay products such as vinyl windows from raw sheets, melting the raw metal for the aluminum materials we use, and blending the raw materials for vinyl.
Even the development and manufacture of components, which constitute the backbone of our products, is carried out in-house. In addition, an in-house division called Machinery and Engineering is responsible for the development and manufacture of equipment for making our products. We are working to further enhance our technological competitiveness through seamless collaboration between the Machinery and Engineering Department and the research and manufacturing divisions.
We are also deploying technology developed in Japan overseas, such as by introducing a labor-saving production line from Japan at YKK AP AMERICA's new vinyl window plant. Going forward, we will pursue "smart factorization" and aim to improve productivity through DX.
Logistics
YKK AP aims to promote logistics efficiency and productivity improvement to realize sustainable logistics.
Specifically, we have introduced a "unit load" system that efficiently transports cargo in units such as pallets and containers, enabling efficient loading and unloading that does not rely on driver experience and intuition. In addition, "Y-Caps", a proprietary system designed to efficiently load pallets onto truck beds, identifies the optimal combination of products and pallets to improve truck loading efficiency and enable optimal dispatch management. Moreover, in order to reduce work hours associated with various logistics processes, we are pursuing sustainable logistics through joint transportation with other companies, thereby reducing drivers' time commitment.
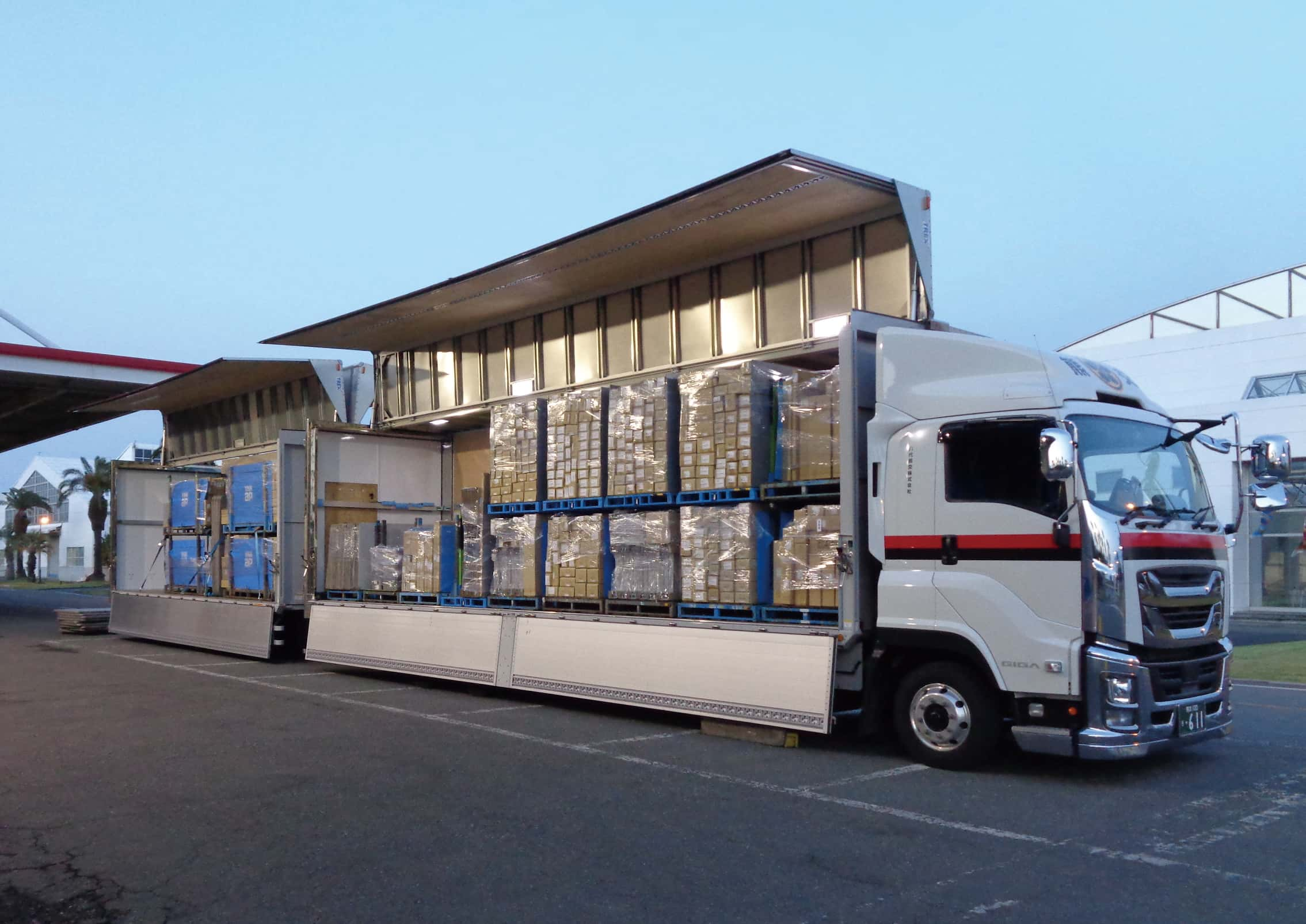
Unit loading facilitated by the introduction of the proprietary "Y-Caps" system
In FY2023, we opened the Tokyo Metropolitan Area DC, a storage-type logistics site for residential windows, doors, and exterior products.
Until now, products for immediate delivery in the Tokyo metropolitan area have been sent from regional manufacturing and logistics sites in the evening of the day the order is received, arriving during the night at the Tokyo Metropolitan Area TC (Transfer Center) (Saitama Prefecture), a pass-through logistics center, from where they are sorted and delivered.
The Tokyo Metropolitan Area DC ensures lead times and reduces the number of overnight long-distance shipments through inventory management based on demand forecasts in which shipment status is subdivided by item and by area.
Shelf-transporting robots have been installed on the premises, and a Goods To Person (GTP) system, in which robots carry inventory storage shelves to the operators, is in operation.
Workers can perform picking and sorting for 100 trucks at once while remaining in their fixed positions, leading to labor and personnel savings. The same technology is also scheduled for introduction at a new vinyl window plant in the U.S.A., which began operations in December 2023.
Going forward, we will continue to promote logistics DX and robotics with the aim of achieving sustainable logistics.
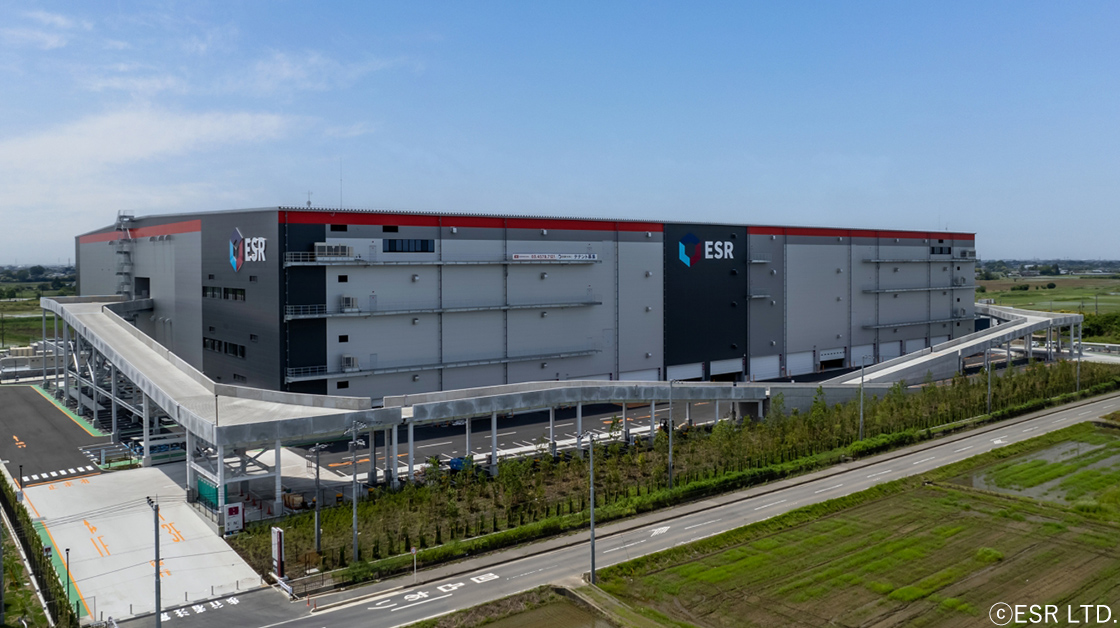
"ESR Kazo Distribution Center 2," where the Tokyo Metropolitan Area DC is located
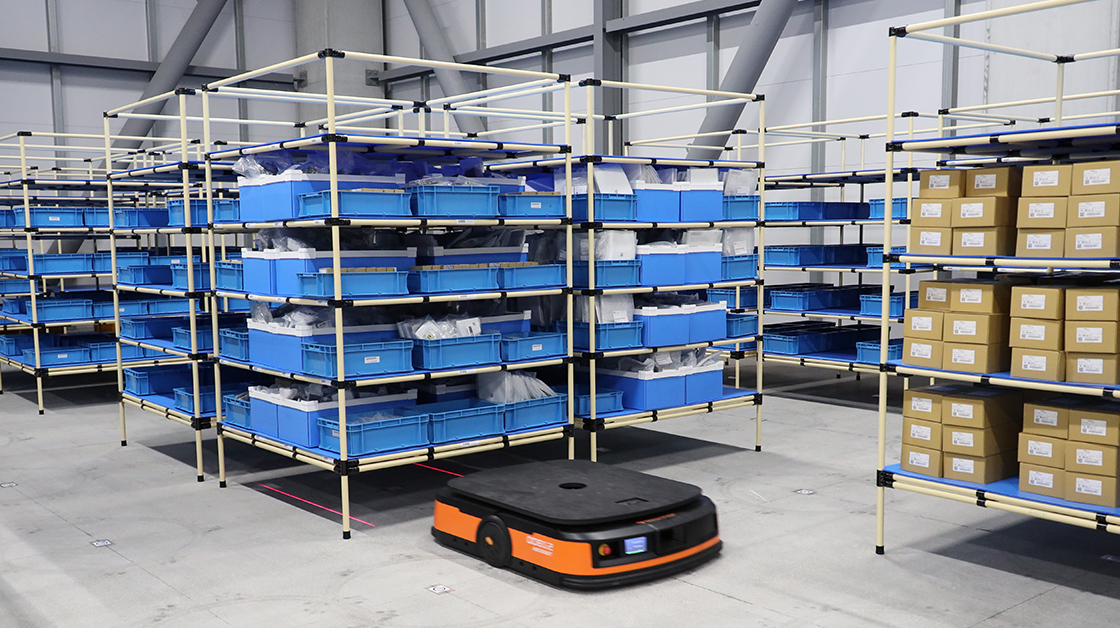
Shelf-transporting robots operating at the Tokyo Metropolitan Area DC
Health and Safety
Another important issue is to create a safe and healthy workplace for employees involved in manufacturing. We are creating a stress-free and fulfilling workplace by installing airconditioning equipment and air-conditioned clothing to combat heat, and improving the environment of the cafeterias and restrooms. To enhance safety, we also continue to conduct regular equipment and machinery safety audits every three years to ensure the intrinsic safety of our equipment.In addition, we have been identifying and improving "shortcut behaviors" and "troublesome tasks" in the workplace in order to eliminate all unsafe practices, and we will provide training to workplace leaders to incorporate hazard prediction into their training, further strengthening safety awareness.