- HOME
- Sustainability
- Environment
- Co-existence with the Environment Initiatives
Co-existence with the Environment Initiatives
EnvironmentAddressing Climate Change
We have set our own greenhouse gas reduction target for FY2030 at 50% below the FY2013 level, which was approved by the international Science Based Targets (SBT) Initiative in February 2021. Our vision "Evolution 2030" calls for an 80% of its eduction by FY2030 and a 100% reduction by FY2040, and we are progressing toward these goals even further ahead of schedule.
We are proceeding with initiatives based on the carbon neutral technology roadmap developed by the "Carbon Neutrality Project, " which is led by an Executive Vice President. We will accelerate capital investment and technological development while reviewing each platform for products and monozukuri.
Furthermore, we will contribute to carbon neutrality not only for our own company but also for the society as a whole by reducing energy used for heating and cooling through the promotion of high-insulation products.
Scope 1 and 2 initiatives
We are working to reduce the amount of fuel and electricity used in our manufacturing processes. In addition to improving the efficiency and energy-conservation performance of our production facilities, we are electrifying our heat source equipment and switching from liquid fuels to natural gas. Furthermore, we are using existing technologies to develop and demonstrate the use of hydrogen, ammonia, and other substances in our gas burners.
We are also working on energy creation from renewable sources, such as solar, hydro, and wind, and as of FY2023, we have increased the amount of renewable energy installed to five times the FY2021 level.
In order to measure our progress in reducing CO2 emissions, we established a database to visualize CO2 emissions by identifying the energy consumption of each piece of equipment at the manufacturing stage.
As of FY2023, we have reduced Scope 1 and Scope 2 emissions by 33% relative to FY2013 levels.
Expand installation of solar power generation, small-scale hydroelectric power generation, and wind power generation​
One of the six working groups of the Carbon Neutrality Project, which is part of our efforts to achieve carbon neutrality, the Energy Creation Working Group (WG) is promoting the introduction of in-house use of renewable energy on the company's own premises. To date, a total of 9,792 kW of solar and small-scale hydroelectric power generation has been installed at nine locations in Japan and overseas. Furthermore, we will accelerate the installation of renewable energy with the goal of expanding energy creation to a total of 15,300 kW by FY2024 and reducing CO2 emissions by 7,900 tons vs. FY2020.
We are also working to further expand the use of wind power along the coast by conducting installation trials.
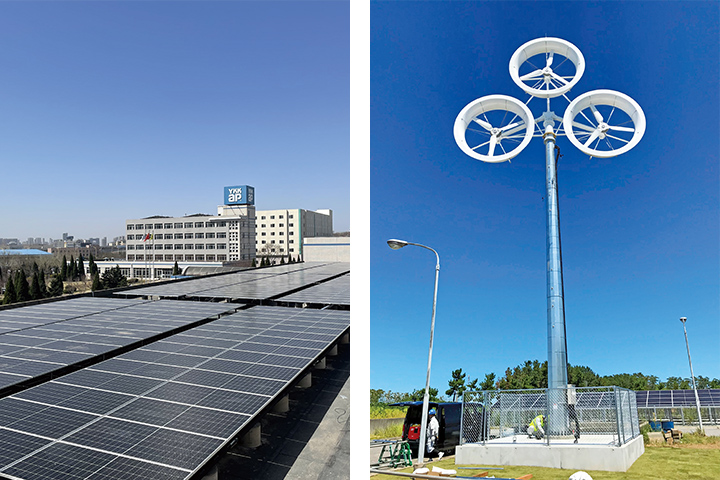
Left: are solar panels installed at DALIAN YKK AP CO., LTD.
Right: is wind power generation equipment installed at the Kurobe Ekko Plant
Scope 3 initiatives
Scope 3 emissions account for the majority of the CO2 emissions associated with YKK AP's business activities across the supply chain as a whole. Of these, emissions from the procurement of raw materials for products account for 80% of the total. In particular, the procurement (mining, refining, and overseas transportation) of aluminum ingots used for aluminum products and other products has a significant impact, and increasing the utilization rate of recycled materials (re-used raw materials such as aluminum scrap recovered from the market) will have the greatest impact toward achieving carbon neutrality. All aluminum scraps generated in the manufacturing process are reused, and we have already achieved an internal recycling rate of 100%.
Furthermore, we are aiming to achieve a 100% aluminum recycling rate for materials on the market generated outside the company, and have improved this rate to 33% as of FY2023.
We are involved, as the lead company, in the "Creation of a Toyama Resource Recycling Society Model," an industry-academia fusion hub concept project to revitalize aluminum-related industries in Toyama Prefecture, led by the University of Toyama. In this way, we are conducting in-depth technical development of aluminum recycling through collaboration between industry, government, academia, and the private sector.
In regard to logistics, as of FY2023 we have introduced 15 double-trailer trucks for transportation over land, increasing the amount of cargo transported at once by 1.8 times the previous level. By introducing "trunk line relay transportation," which includes consolidating transportation routes and improving loadability by combining partial loads, "secondary delivery," which includes joint delivery and alternate-day delivery, and "modal shift," which includes using railroad containers, we are making ongoing efforts to reduce CO2 emissions.
As of FY2023, we have reduced Scope 3 emissions by 10% relative to FY2013 levels.
Introduction of YKK AP's first aluminum recycling furnace
YKK AP is introducing recycling furnaces in order to increase the company's ratio of input of market-obtained recycled materials to the input of aluminum raw materials. While ordinary melting furnaces can melt large quantities of market-obtained recycled materials by heating them with a burner, adding large quantities of such materials leads to oxidation and increased aluminum depletion. A dedicated recycling furnace, which uses a different method than a melting furnace, can reduce the amount of wear and tear during aluminum melting.
In September 2023, the Shikoku Plant installed YKK AP's first recycling furnace and began operation. By combining this recycling furnace with our melting furnaces, we were able to increase the recycling rate for market-obtained materials generated outside the company, reaching 50% in a single month in December 2023.
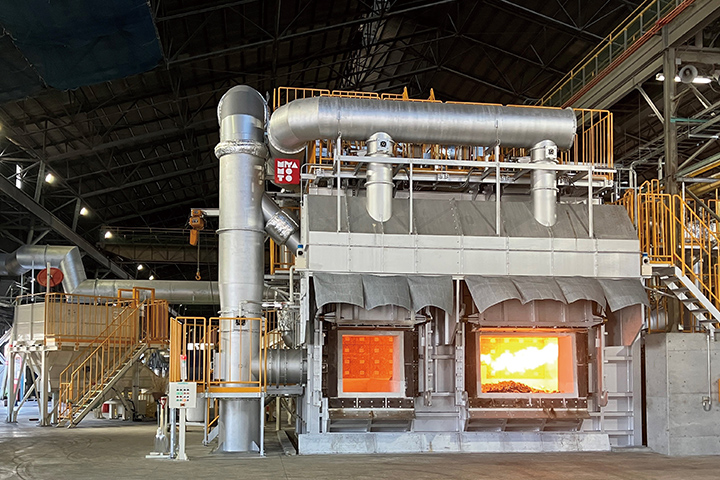
Recycling furnace at the Shikoku Plant.
At the back left is an automatic material feeder
Taking on the Challenge of a Circular Economy
In pursuit of realizing a circular economy, we promote activities that are in line with the Three Rs (Reduce; Reuse; and Recycle) to reduce waste materials, and reuse and recycle materials.
We aim to improve recycling rates (zero landfill) and reduce waste output by 40% from our business activities. We focus on valorizing and reusing waste and enhancing resource efficiency.
We have already achieved the 100% recycling rate for industrial waste generated from manufacturing sites in Japan and continue our efforts to reach 100% domestically and internationally.
To "reduce industrial waste", we prioritize reducing plastic packaging materials through simplifying packaging, shifting them to returnable ones, and standardizing packing materials. Additionally, we have introduced facilities at the Kurobe Ekko Plant to produce RPF (refuse-derived paper and plastics-densified fuel) from waste plastics like film and laminate, along with recycled paper and wood chips, further promoting waste valorization.
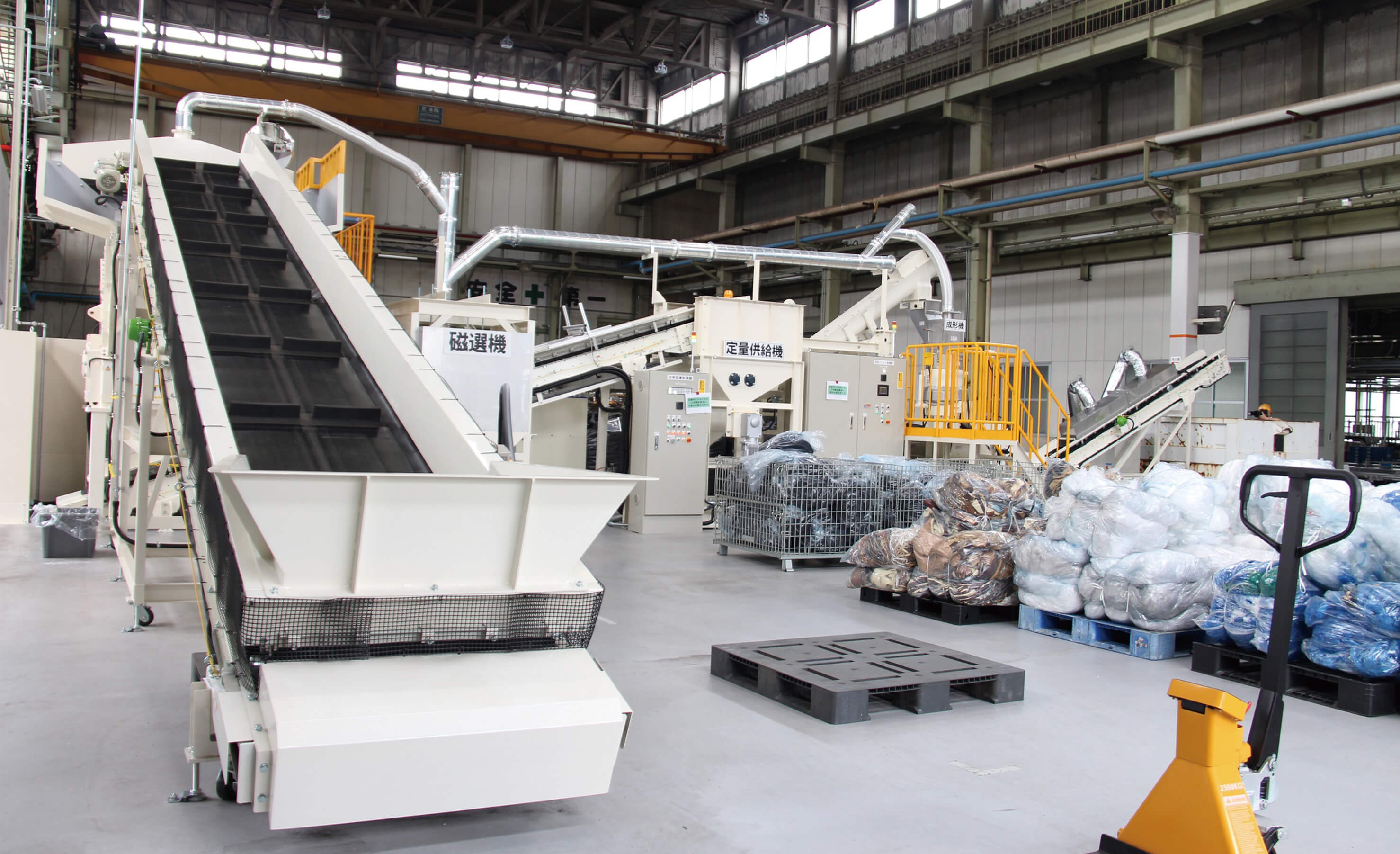
RPF Manufacturing Facility (Kurobe Ekko Plant)
Toward improved vinyl recycling rates
We are also actively engaged in recycling the vinyl produced during the manufacturing process for vinyl windows and after use. We have installed crushing and sorting equipment at each of our vinyl window manufacturing sites, and by reusing the materials as raw materials for vinyl profiles and gaskets* for insulating glass, our internal recycling rate had improved to approximately 45% by the end of FY2023.
- Parts used to fit glass into sashes
Social implementation of vinyl window recycling
In order to implement recycling of vinyl windows circulating on the market, thereby reducing the amount disposed of in landfills, YKK AP is participating as a member of the "Vinyl Window Recycling Committee," which is formed mainly of industry associations. The association is engaged in industry-government-academia collaboration to establish a system to collect and recycle vinyl windows after use.
Furthermore, in January 2024, it announced its "Vision for Vinyl Window Recycling." This vision sets goals such as bringing recycled products to market by the end of 2024 and utilizing 10,000 tons of recycled materials annually by 2030, and is stepping up the pace of these initiatives.
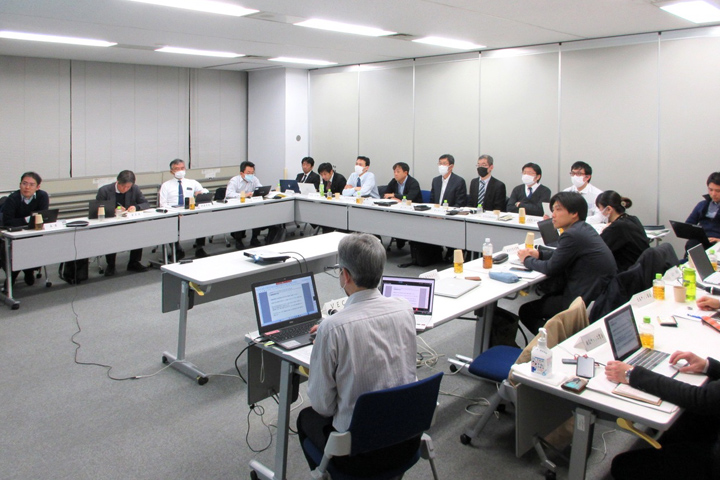
Regular meeting of the Vinyl Window Recycling Committee
Implementation of Guidelines for Environmentally Friendly Design
To minimize CO2 emissions throughout the supply chain, YKK AP applies its "Environmentally Friendly Design Guidelines" during product development. We evaluate and improve products with respect to the following five items over the product lifecycle: "visualization of CO2 emissions," "standardization of packaging materials," "visualization of environmentally hazardous substances," "ease of disassembly and separation," and "environmentally friendly design guidelines and evaluation methods." In particular, with regard to packaging materials, we are expanding the use of reusable packaging materials and reducing the amount of plastic used. In FY2023, CO2 emissions were calculated when developing new products, and further reductions were explored.