
By bringing installation technician expertise and monozukuri together, YKK AP is focusing on human resource and product development to enhance exterior product quality and streamline installation.
“We Build a Better Society Through Architectural Products.” This is YKK AP’s Purpose and the meaning of our existence as we conduct our business of developing, manufacturing, and selling windows, doors, interior architectural products, exterior products, curtain walls, and other items. Our job involves more than just making products—these items only function when installed at a residence, building, or other site where they are used by customers. In other words, installation greatly affects the final quality, as much as the product itself. Rather than YKK APP employees, this process is performed by installation technicians. However, a shortage of product installation technicians is a major problem facing the construction industry. YKK AP is making exterior product development efforts to resolve these challenges and improve installation quality.
The exterior product category includes fences for property and road boundaries, decks installed in yards, carports to protect customers’ beloved vehicles, and balconies that provide spaces to dry laundry and relax. Exterior planning is part of building a home, but sometimes the construction process starts with planning the layout and other portions of the building, and the exterior is planned separately or put off until later. Despite this, exterior items are very important—they help maintain privacy, and exterior designs should harmonize with and be integrated into the building. And because people are spending more time at home due to the COVID-19 pandemic, demand is growing for attached yards and other exterior products to create enjoyable, private outdoor spaces.
While products like windows and doors are attached to the existing building frame, exterior products are installed in empty spaces. Technicians must have skills to install these in three dimensions, including length and height. Requirements differ at installation sites, such as lot shapes, elevation differences, and distances from adjoining properties. In some cases, installation requires advanced skills backed by ample experience. And because exterior items are exposed to wind and rain in harsh outdoor environments, they must be installed with a high level of quality to prevent flooding and other problems. YKK AP is focusing on both human resource development and product development in light of these unique environments and challenges.

YKK AP exterior products
Passing down installation technician expertise: human resource development
YKK AP opened the DO SPACE Ageo exterior installation technique training facility in January 2020, with a curriculum primarily focused on developing human resources who install our exterior products. The person in charge of operating this facility is Yoshihisa Kanata, leader of the Technological Base Strengthening Team, Exterior Technology Development Office, Human Resource Development Project. We spoke with Kanata about how a product manufacturer started this training facility for installation technicians, and his thoughts about the kind of training it provides.
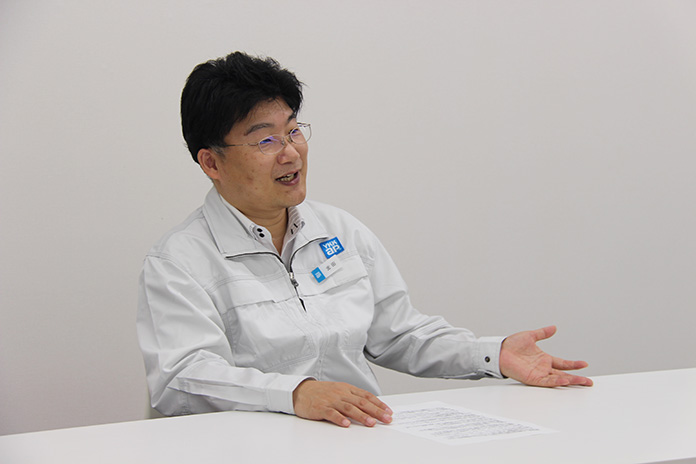
The inability to deliver products could become a future crisis
Fewer exterior product installation technicians are learning their trade through a master-pupil relationship today, and more self-employed technicians are reaching their 60s and 70s without anyone to take over their business. Manufacturers cannot deliver products to users without opportunities and environments to train skilled technicians who can install their products on-site. YKK AP founded DO SPACE Ageo to develop installation technicians, improve their abilities, and help them pass on their advanced skills, with the aim of continued growth in the exterior product industry.
Training that goes beyond product assembly
Our goal is for technicians to master an overall range of product installation knowledge and skills, from on-site surveys to assembly, installation, and maintenance. After talking with installation technicians about their processes and expertise, we’ve developed and offer a curriculum with text and visual depictions of these advanced skills, including videos. When installing exterior products, the difficulty depends on where and how the technician begins the process, which involves three dimensions: height, width, and depth. For instance, installation manuals say to measure the horizontal and vertical lengths, but these methods differ according to the job site environment. Technicians have to decide how they will do the work—manuals can’t cover everything, and some products aren’t always installed in the same places. That’s why our training isn’t focused only on product installation techniques; we also teach about the preparatory steps (work plan) prior to installation. An example is the process of marking reference lines for the horizontal and central positions. We’ve learned about these things from installation technicians, and we incorporate them into our training program so we can teach accurate, efficient installation.
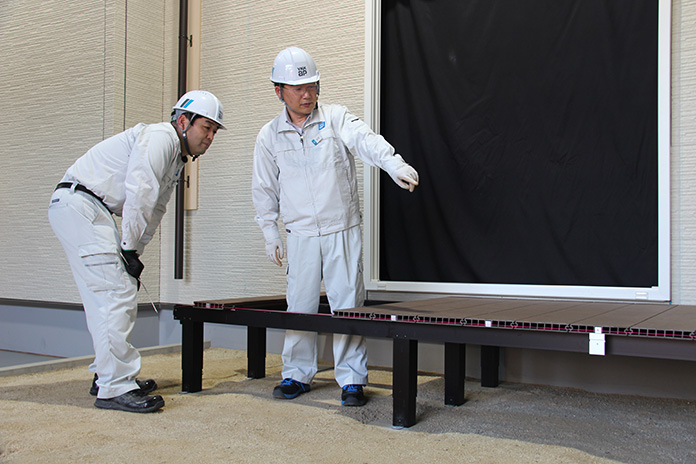
Marking reference lines to install a deck
Understanding what is impossible
Along with planning, we believe it is important for technicians to learn from hands-on experience. Even with an intellectual understanding of the installation process, experience is necessary for learning how it feels to handle these products, including their actual size and weight. Two 20-kilogram material pieces may feel different according to their length and shape. By experiencing what it’s like to install these, students come to understand what is and what isn’t possible. Mistakes they make at the facility allow them to succeed at real job sites. The things they experience during their training become a foundation for confident on-site work.
Nationwide human resource development
DO SPACE Shikoku is our second training facility, opened in September 2022 at the Shikoku Plant in Kagawa Prefecture. Its curriculum is mainly for installation technicians at architectural product distributors. If we created a short-term program, it could help resolve the shortage of installation technicians, which would be significant for the entire industry. We are planning to establish training sites in other areas in the future, which includes developing YKK AP human resources who can teach at these facilities. If there were more exterior product installation technicians across Japan who have mastered these advanced skills, I think we could maintain a high level of installation quality and deliver products for comfortable, fulfilling lifestyles.
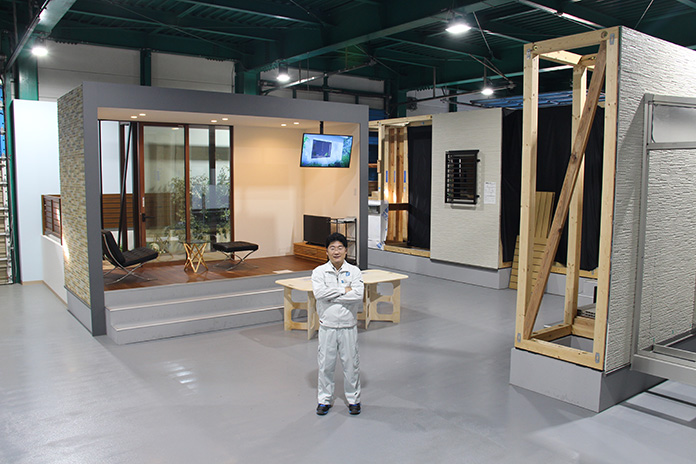
At DO SPACE Ageo, our exterior installation training facility
Taking on the challenge of maintaining installation quality through product appeal: product development
Among YKK AP’s product lineup, exterior products are particularly affected by the quality of their installation. This is why we are developing products that don’t depend as much on technician skills. Shingo Horie is head of the Carport and Terrace Product Development Office, Exterior Product Development Group, Product Development, Residential Business, Research & Development. He described the carport development efforts that take installation technicians into account, not just the customers who use these products.
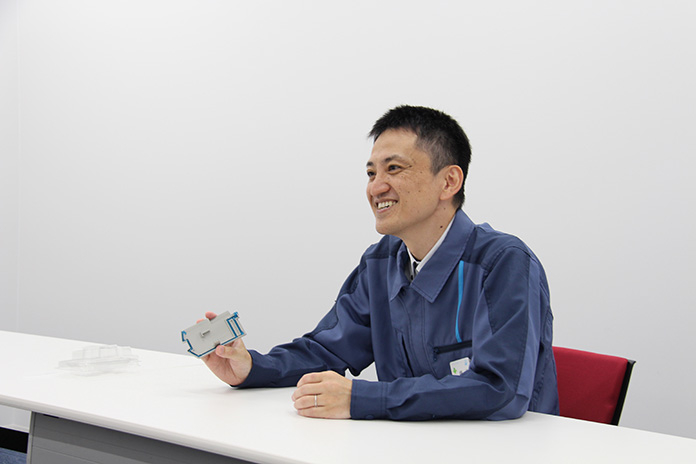
Preventing leaks through creative measures and improvements that do not depend on technician skills
Carports protect our customers’ beloved vehicles from dirt and deterioration by shielding them from the elements, including rain, snow, and the sun. Carports must be installed with a high level of quality to accomplish this job. One important point is the sealing process. The technician applies a paste sealant to the caps where parts are joined, which provides waterproof and water-blocking properties. Because this is done by hand, the finished quality depends greatly on the skills of the technician, and quality can easily vary for the same product. There are cases when water has leaked because the technician didn’t use enough sealant or didn’t apply it consistently. Leaks—which are actually the most common issue with carports—are usually problems with the sealing process. We began working to develop a sealing-less cap as a way to prevent leaks.
Striving for a new material that meets quality standards
To eliminate the need for sealant, we came up with the idea of using a water-blocking material that is applied to the cap before assembly. We thought we could achieve the same water-blocking performance by adhering this material between the parts.
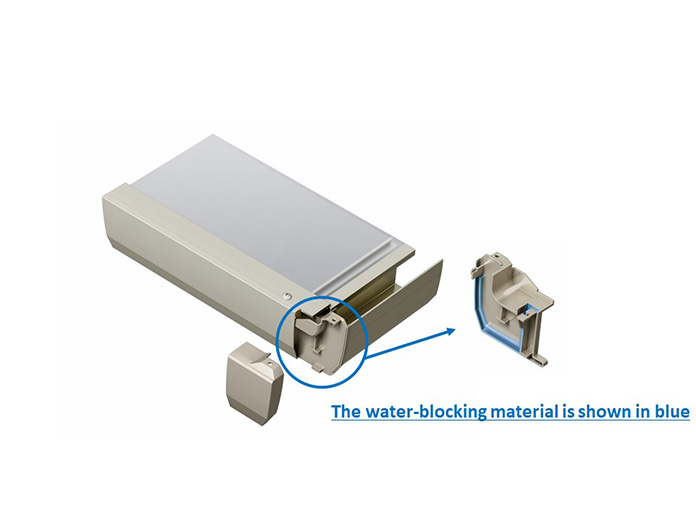
Cap with water-blocking material that is installed in the carport roof corner
There were many different issues in making this idea a reality, and many things to consider. For example, we had to think about what material could meet the quality standards, including water-blocking properties and durability. We had to come up with part shapes where the water-blocking material could be applied with automated equipment on the production line. We also had to think about whether it was easy to assemble, and how to package the parts so none of the material got on the packaging.
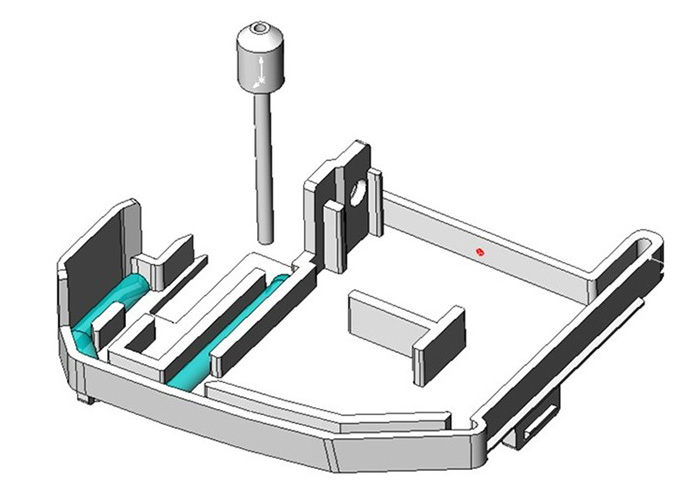
Automated equipment applying water-blocking material to the parts
To maintain quality, the automated equipment must be able to steadily apply a suitable amount of water-blocking material at the determined location. At first this didn’t go well because the amount applied was not consistent. But with repeated trials, we were able to adjust the cap groove shape to apply the water-blocking material in a stable fashion and maintain the location.
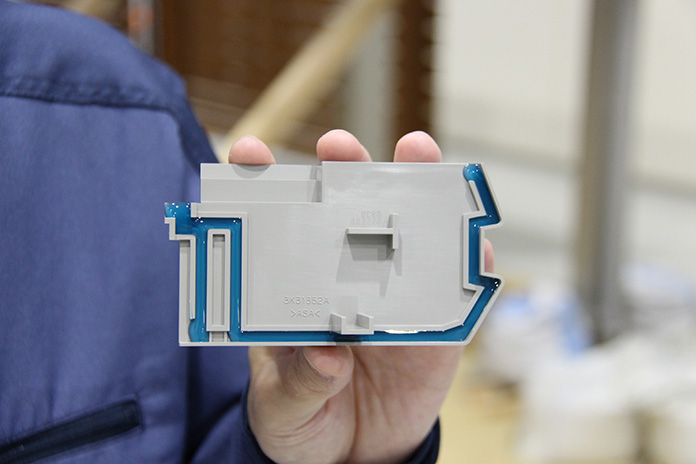
Cap groove filled with water-blocking material
We finalized the sealing-less cap by solving each of these issues. We couldn’t have done it without cooperation from the Fabrication Technology Division that evaluated the new material’s performance, as well as the plant’s Equipment Design Division. Three divisions joined together to develop the material, parts, and manufacturing equipment. I believe this type of monozukuri can only be accomplished through the integrated production system that is YKK AP’s forte.
The satisfaction of creating a defect-less product
Our sealing-less cap was adopted for the Frouge FIRST polycarbonate roof released in 2019, followed by the Arius series. By creating other sealing-less parts, we’ve achieved a totally sealing-less installation process. I feel very satisfied because there hasn’t been one leak at a sealing-less cap since its introduction. We are working for better quality by using this technology in terraces and other exterior products besides carports, and we are also raising awareness of our sealing-less products through training events at job sites.
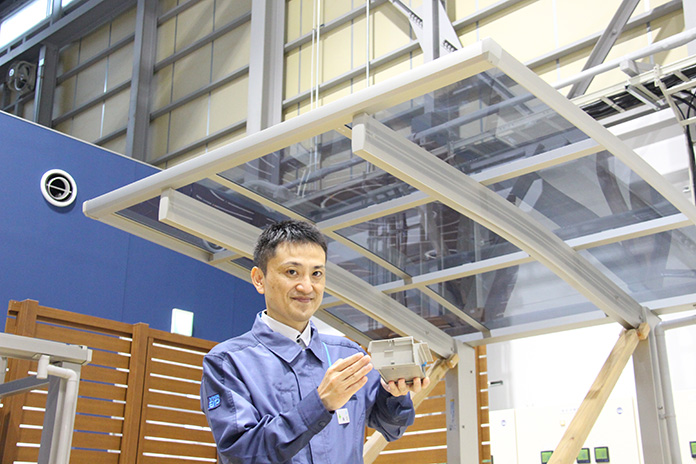
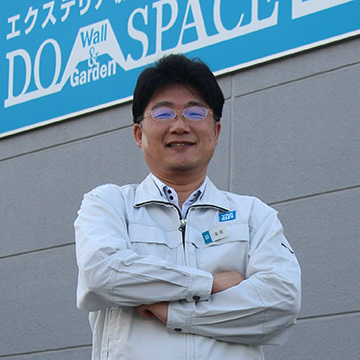
Yoshihisa Kanata
Joined YKK AP in 1993. Was involved in system development for 10 years in the former Information Systems division. Worked in Exterior Planning, Residential Products from 2013 and in the Business Process Development Office, Business Development, Exterior Business from 2017. Since 2019, in his current division he has helped open and operate DO SPACE Ageo to improve exterior installation skills.
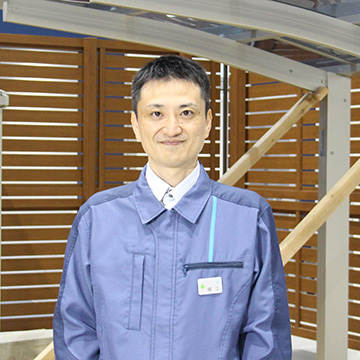
Shingo Horie
Began working at YKK AP in 2004, and developed carport products until FY2008.
Has applied his past knowledge to terrace product development since FY2009.
Share this article
- SNS Link X X Share
- SNS Link Facebook Facebook Share
- SNS Link LinkedIn LinkedIn Share
- SNS Link LINE LINE Share
- Copy Link Copy Link Copy Link Copied Link
Related stories
-
Supporting Product Quality at YKK AP — The Role of the Field Engineer, from Installation Support to Gathering Feedback from Work Sites and Making Improvements
- Residential Business
- Exterior Business
- Technology
- Installation
-
The installation training network began as a challenge to solve the shortage of sash and curtain wall installation technicians. Taking on challenges in collaboration with partners, and going from Japan to overseas
- Technology
- Installation
- Solving Social Issues
- Story of Project
-
Establishing a digital R&D center in the U.S.A. What is YKK AP's digital strategy for smart factories?
- R&D
- Technology
- Installation
- DX